The manufacturing industry has undergone tremendous changes over the past century. From initially using simple mechanical setups to process handmade parts with low precision requirements, to today’s highly automated manufacturing processes, the evolution has profoundly transformed the face of manufacturing. As technology advanced, especially in mobility and computer technology, the demand for precision parts in manufacturing has grown, particularly in the aerospace and automotive sectors. This led to the emergence of precision machining technology, which has become a core component of the manufacturing industry.
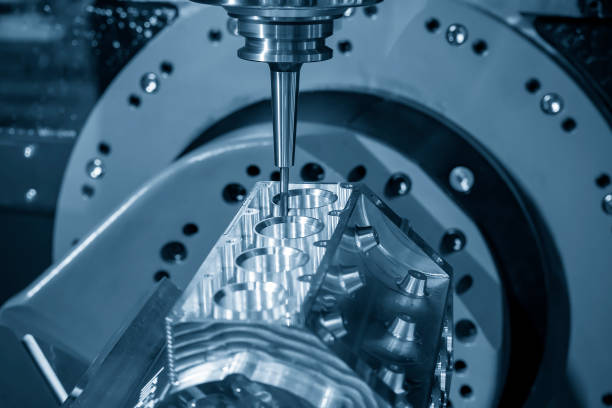
Key Concepts in Precision Manufacturing
The rapid development of the manufacturing industry is mainly attributed to the introduction of automation technology and the advancement of precision machining techniques. Below, we will explore the key concepts of precision machining and its applications in modern manufacturing.
Precision Machines
Precision machines are designed to manufacture parts with extremely high accuracy and strict tolerances. These machines are typically guided by Computer Numerical Control (CNC) technology, capable of performing precise cutting, milling, turning, or drilling operations. Common precision machines include CNC milling machines, CNC lathes, and Swiss-type lathes.
Precision Manufacturing
Precision manufacturing refers to a set of practices and processes used in the manufacturing industry to produce parts with high precision. It involves the use of precision machines, stringent quality control measures, and advanced technologies to ensure that products consistently meet exact specifications with minimal variation.
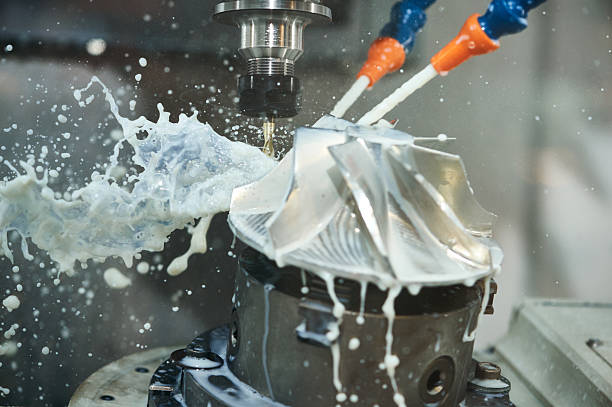
CNC Manufacturing
CNC manufacturing employs Computer Numerical Control (CNC) machines that are programmed to perform specified operations with high precision and efficiency. CNC technology simplifies the production process and enhances the quality and consistency of manufactured parts.
Computer-Aided Design (CAD)
Computer-Aided Design (CAD) plays a crucial role in manufacturing. CAD software is used to create detailed and accurate digital models of physical components, allowing designers and engineers to build, modify, analyze, and optimize designs before producing any physical prototypes. Common CAD tools include AutoCAD and SolidWorks.
Importance of Precision Machining
Precision machining significantly determines the operational integrity, safety, and market viability of manufactured products. Precision is critical in ensuring that engineering components work according to design specifications without failure. This is especially important in fields such as aerospace and medical devices, where safety is paramount, and even minor dimensional deviations can lead to severe consequences, including life-threatening system failures.
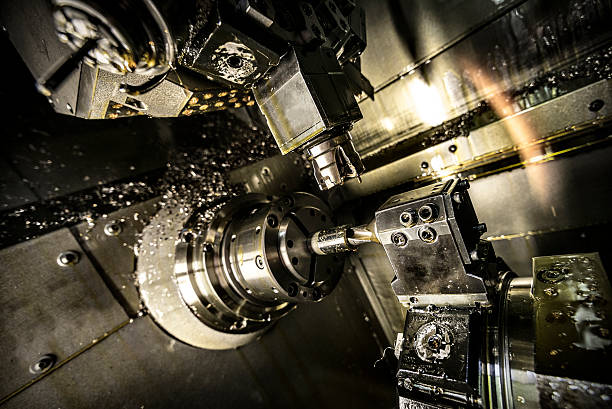
Additionally, advancements in high-tech components heavily rely on precision machining technologies. This technology is essential for manufacturing complex and miniaturized components critical for emerging technologies such as electronics and quantum computing.
Overview of the Precision Machining Process
Precision machining is a series of meticulously planned steps that ultimately produce parts that exactly match their design.
- Design Using CAD: Engineers use CAD software to create graphical models, laying the foundation for the design.
- Conversion to CAM: CAD models are converted into machine-readable code, such as G-code and M-code.
- Material Selection and Preparation: Appropriate materials are chosen and prepared based on requirements.
- Precision Machine Setup: Machines are calibrated, and fluid and coolant levels are checked.
- Machining Execution: The machining process is monitored and adjusted to ensure smooth operation.
- Post-Processing Steps: Additional finishing processes like polishing or grinding may be needed, followed by quality assurance checks.
Learn how to choose a CNC machine.
how to make a precision machining parts.
Types of Precision Machining Equipment
CNC Milling Machines
CNC milling machines use rotating tools to remove material from the workpiece, performing various operations such as pocket milling, contour milling, and surface contouring.
CNC Torna Tezgahları
In CNC lathes or turning centers, the workpiece rotates against a fixed cutting tool, creating precise symmetrical shapes.
Swiss-Type Lathes
Swiss-type lathes differ from traditional lathes in that the headstock moves linearly rather than being fixed, allowing for precise movement of the workpiece. These machines are ideal for producing very small and complex parts.
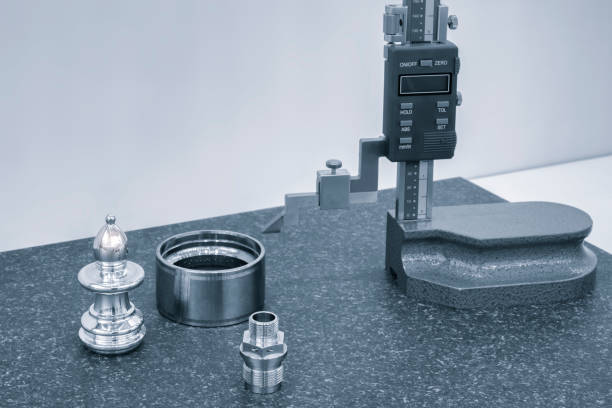
Advantages of Precision Machining Technology
Manufacturers turn to precision CNC machining technology for several benefits:
- High Precision and Strict Tolerances: Standard tolerance levels are around 0.005 inches.
- Complexity and Manufacturing Flexibility: Precision machining allows manufacturers to create complex geometries with high precision and repeatability.
- Efficiency and Speed: CNC significantly accelerates machining time.
- Improved Quality and Reliability: Computer control ensures consistent quality for each part.
- Maliyet-Etkililik: Despite high initial setup costs, precision machining is cost-effective for both large-scale production and custom manufacturing.
Outsourcing Precision Machining
Producing precision-machined products can be challenging, especially when demand is infrequent. Outsourcing precision machining is a practical option. GCH Process offers one-stop precision machining service solutions, ensuring each component meets stringent quality standards, including precision CNC milling, turning, grinding, and EDM, with tolerances up to 0.01mm.
Sonuç
Today’s machines are complex assemblies composed of numerous tiny parts, each requiring perfect synchronization to function as a unified whole. Precision machining is crucial in ensuring these components are manufactured to exact dimensions. As the world continues to advance toward more sophisticated technologies and microsystems, the importance and application of CNC precision machining will only increase. Contact GCH Process to learn how we can support your manufacturing goals with precision and reliability.