Here’s an expanded version of your article, maintaining relevance while adding depth and additional perspectives:
Advanced Applications and Future Trends in Custom CNC Machining for Complex Geometries
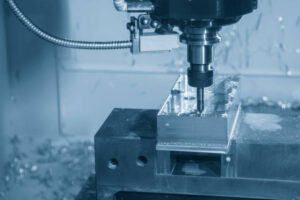
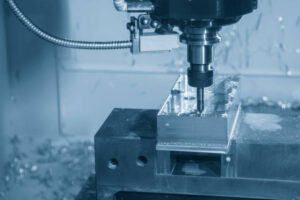
The Evolution of CNC Machining Technology
As manufacturing demands continue to evolve, CNC machining technology has undergone significant advancements. Modern CNC machines now incorporate multi-axis capabilities, allowing for simultaneous movement across 5 or more axes. This enhancement enables the production of increasingly complex geometries with a single setup, reducing production time and improving accuracy.
Key Technological Advancements:
- Hybrid Manufacturing Solutions
- Combination of CNC machining with additive manufacturing
- Integration of in-process inspection systems
- Real-time quality control and adjustment capabilities
- Smart Manufacturing Integration
- IoT sensors for real-time monitoring
- Predictive maintenance systems
- Digital twin technology for process optimization
- Advanced Control Systems
- Adaptive control algorithms
- Dynamic error compensation
- Enhanced surface finish capabilities
Material Processing Capabilities
Modern CNC machining systems excel in processing a wide range of materials:
Metais:
- Aluminum alloys
- Titânio
- Aço inoxidável
- Exotic alloys
- High-temperature superalloys
Plásticos:
- Engineering plastics
- High-performance polymers
- Medical-grade materials
- Composite materials
Specialized Materials:
- Ceramics
- Glass
- Advanced composites
- Novel alloys
Industry-Specific Applications
Aerospace Industry:
- Turbine components
- Structural elements
- Landing gear components
- Satellite components
- Precision mounting brackets
Medical Industry:
- Implantable devices
- Instrumentos cirúrgicos
- Diagnostic equipment components
- Custom prosthetics
- Medical imaging equipment parts
Automotive Industry:
- Prototype components
- Performance parts
- Custom racing components
- Electric vehicle components
- Precision transmission parts
Electronics Industry:
- Heat sinks
- Chassis components
- Testing fixtures
- Precision mounts
- Custom enclosures
Advanced Manufacturing Processes
Multi-Axis Machining:
- 3+2 axis machining
- 5-axis simultaneous machining
- Multi-tasking machine capabilities
- Turn-mill operations
- Complex surface machining
Precision Engineering:
- Micro-machining capabilities
- Ultra-precise tolerances
- Surface finish optimization
- Complex feature creation
- Intricate detail management
Quality Assurance Systems:
- In-process measurement
- Automated inspection
- Statistical process control
- Documentation and traceability
- Compliance verification
Additional Case Studies
Case Study 3: Electric Vehicle Components
A leading electric vehicle manufacturer required complex cooling channels in their battery housing components. The design featured intricate internal geometries that were crucial for thermal management. Using advanced 5-axis CNC machining, the manufacturer successfully produced components with optimal cooling efficiency while maintaining structural integrity.
Case Study 4: Satellite Components
A space technology company needed ultra-precise components for satellite communication systems. The parts required extremely tight tolerances and complex geometric features. Through specialized CNC machining processes and advanced quality control systems, the components were manufactured to exact specifications, ensuring reliable performance in space applications.
Future Trends and Innovations
- Artificial Intelligence Integration
- Machine learning for process optimization
- Automated programming systems
- Predictive quality control
- Smart toolpath generation
- Adaptive manufacturing processes
- Sustainable Manufacturing
- Reduced material waste
- Energy-efficient operations
- Environmentally friendly coolants
- Recycling systems integration
- Green manufacturing practices
- Digital Manufacturing Ecosystem
- Cloud-based manufacturing
- Remote monitoring capabilities
- Digital workflow integration
- Connected factory systems
- Real-time production analytics
Choosing a CNC Machining Partner
Enhanced Selection Criteria:
Capacidades técnicas
- Machine park specifications
- Software capabilities
- Material processing expertise
- Quality control systems
- Production capacity
Industry Experience
- Sector-specific knowledge
- Compliance certifications
- Project portfolio
- Technical expertise
- Innovation capabilities
Service Excellence
- Project management
- Communication systems
- Documentation
- Support services
- Response time
Value-Added Services
- Design assistance
- Material selection support
- Post-processing capabilities
- Assembly services
- Logistics support
Cost Optimization Strategies
- Design for
Manufacturability
- Early engineering involvement
- Material optimization
- Process efficiency
- Tooling considerations
- Setup reduction
Production Planning
- Batch optimization
- Machine utilization
- Tool life management
- Material handling
- Quality control integration
Process Optimization
- Cycle time reduction
- Setup time minimization
- Tool path optimization
- Cutting parameter optimization
- Quality improvement
Future Considerations
As manufacturing technology continues to evolve, several factors will influence the future of CNC machining:
Industry 4.0 Integration
- Digital transformation
- Connected systems
- Data analytics
- Automated decision-making
- Smart manufacturing
Sustainability Requirements
- Energy efficiency
- Waste reduction
- Environmental compliance
- Resource optimization
- Green manufacturing
Market Demands
- Increased customization
- Shorter lead times
- Higher quality standards
- Cost competitiveness
- Global competition
Conclusão
The field of custom CNC machining for complex geometries continues to evolve, driven by technological advancement and market demands. Success in this field requires staying current with emerging technologies, maintaining high-quality standards, and fostering strong partnerships with clients. As manufacturing requirements become more sophisticated, the role of custom CNC machining will become increasingly crucial in meeting these challenges while providing cost-effective, high-quality solutions for complex manufacturing needs.