Introduction
Usinage de précision is a highly specialized process that involves cutting materials to exact specifications using computer-controlled machines. This guide explores the intricacies of precision machining, detailing how precision machined parts are made, from design to quality control. Whether you’re looking for insights into precision machining services or aiming to produce precision machining parts, this guide will provide valuable information.
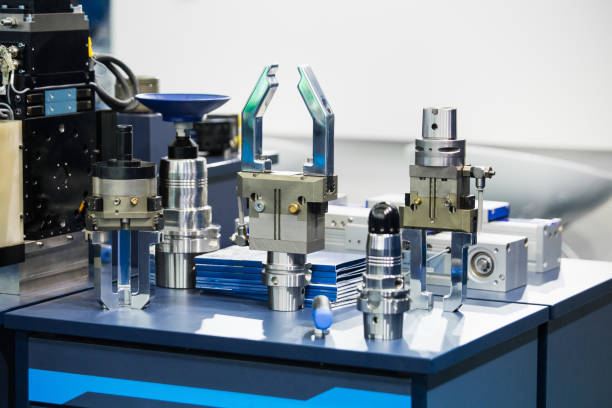
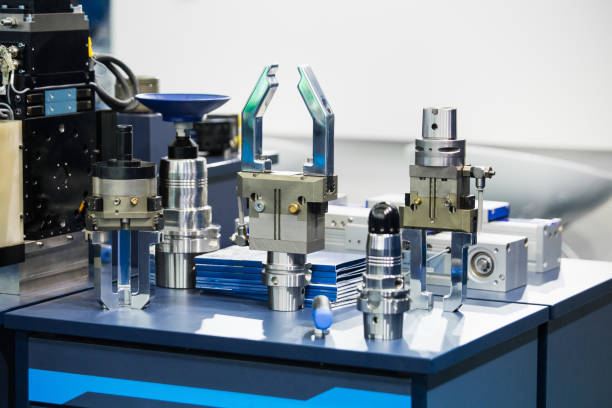
What is Precision Machining?
Precision machining is a manufacturing process that uses computer numerical control (CNC) machines to produce parts with high precision and accuracy. It is crucial in industries like aerospace, automotive, and medical, where tight tolerances and superior finishes are essential.
Key Features:
- Haute précision et exactitude: CNC machines can achieve tolerances as tight as ±0.001 inches, ensuring parts meet exact specifications.
- versatility: Precision machining can be applied to a wide range of materials, including metals, plastics, and composites.
- Répétabilité: CNC machines ensure consistent production of identical parts, critical for mass production.
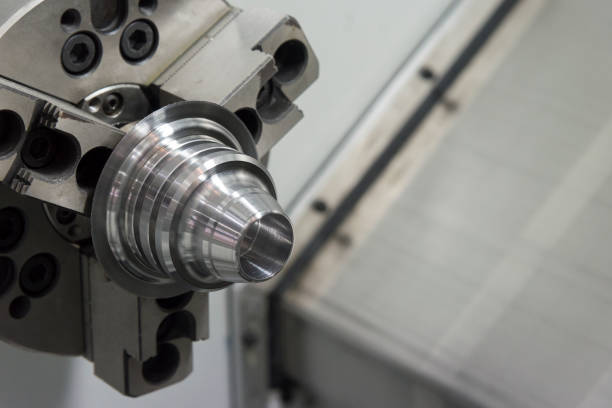
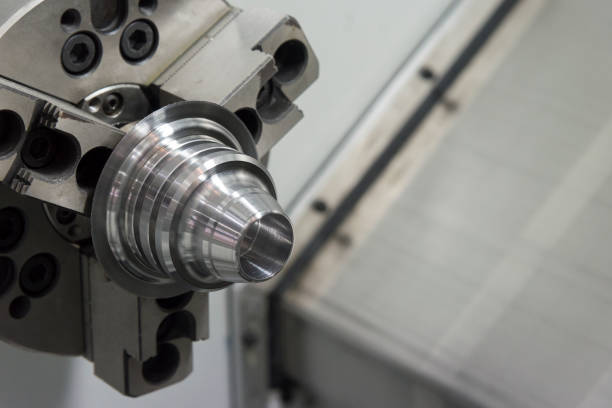
Precision Machining Techniques
Several techniques are employed in precision machining, each serving different purposes. Understanding these techniques is fundamental to selecting the right method for your project.
Tournage
- Purpose: Turning is used to create cylindrical parts, such as shafts, bolts, and nuts.
- Tools: The primary tool is the lathe machine, which rotates the workpiece while a stationary cutting tool removes material.
- Process: The workpiece is clamped in the lathe, and as it rotates, the cutting tool moves along the axis of the workpiece to shape it into the desired dimensions. Turning can produce both external and internal cylindrical surfaces.
Forage
- Purpose: Drilling is used to create precise, cylindrical holes in a workpiece.
- Tools: Drill presses and CNC drilling machines are the main tools used.
- Process: A rotating drill bit is pressed against the workpiece, cutting into the material to create a hole. Drilling can produce a wide range of hole sizes and depths, and it is often followed by processes like reaming or tapping to achieve the final dimensions and finishes.
Fraisage
- Purpose: Milling is used to produce complex shapes and features, including slots, holes, and contours.
- Tools: Milling machines utilize rotating multi-point cutting tools.
- Process: The workpiece is mounted on a movable table, and the cutting tool rotates at high speeds to remove material. Milling can be performed on both flat and irregular surfaces, making it highly versatile. Types of milling include face milling, where the cutting is perpendicular to the workpiece surface, and peripheral milling, where the cutting is parallel to the surface.
Broyage
- Purpose: Grinding achieves high surface finishes and tight tolerances, ideal for finishing operations.
- Tools: Grinding machines use abrasive wheels.
- Process: The abrasive wheel rotates at high speed, and the workpiece is fed into the wheel, removing small amounts of material. Grinding can produce very smooth surfaces and precise dimensions, making it essential for applications requiring high accuracy.
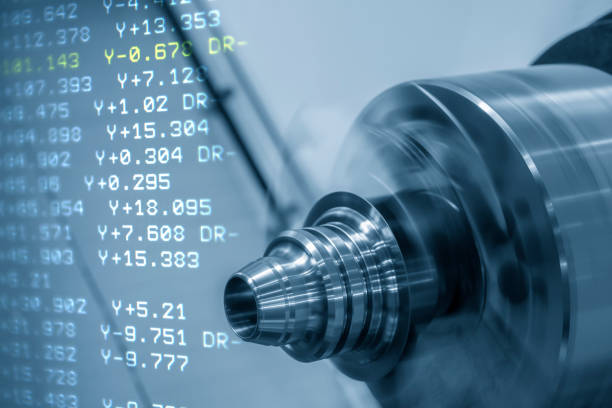
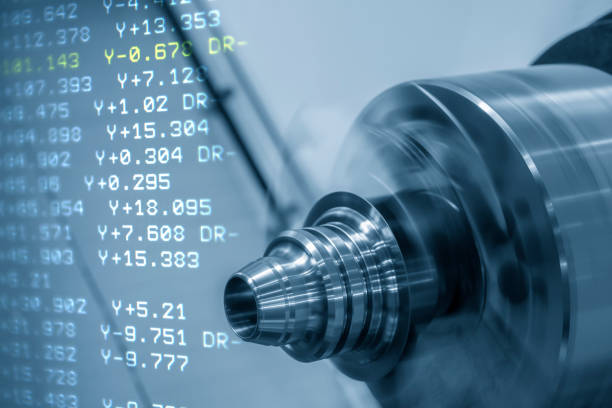
Materials Used in Precision Machining
Precision machining works with various materials, chosen for their specific properties. The choice of material impacts the machining process, tool selection, and final product characteristics.
Métaux
- Aluminium: Known for its lightweight, corrosion resistance, and excellent machinability. Commonly used in aerospace, automotive, and consumer electronics.
- Acier: Offers high strength and durability. Available in various grades, such as carbon steel, stainless steel, and tool steel, each suited for different applications.
- Titane: Valued for its high strength-to-weight ratio and corrosion resistance. Predominantly used in aerospace and medical implants.
Non-Metals
- Plastiques: Lightweight and versatile, plastics like ABS, polycarbonate, and PEEK are used for prototypes, consumer products, and medical devices.
- Ceramics: Extremely hard and wear-resistant, ceramics are used in high-temperature and high-wear applications, such as aerospace and electronics.
- Composites: Combine different materials to achieve desired properties, like strength and lightweight. Common composites include carbon fiber and fiberglass, used in automotive, aerospace, and sporting goods.
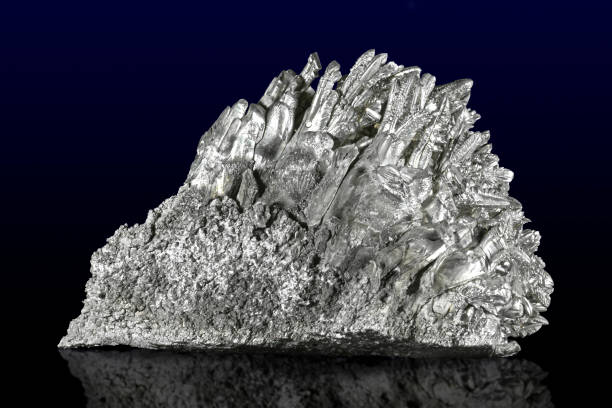
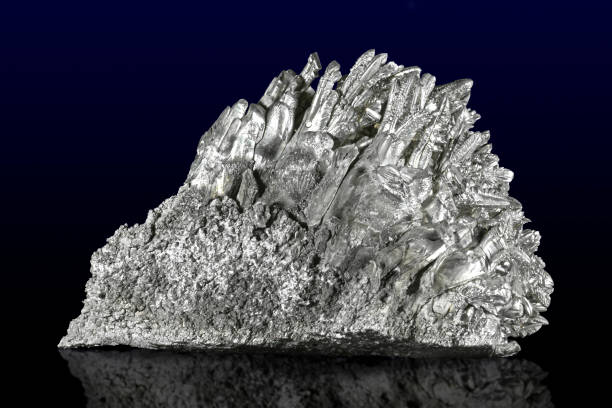
Designing Precision Machined Parts
Creating a detailed design is the first step in precision machining. A well-thought-out design ensures that the parts will meet all functional and aesthetic requirements.
CAD Software
- Purpose: Computer-Aided Design (CAD) software is used to create detailed 3D models of the parts.
- Process: Engineers use CAD software to generate precise drawings, specifying dimensions, tolerances, and surface finishes. Popular CAD software includes AutoCAD, SolidWorks, and CATIA.
Design Considerations
- Tolérances: Define the acceptable variation in part dimensions. Tight tolerances ensure parts fit together correctly but may increase manufacturing costs.
- Finition de la surface: Specifies the texture and smoothness of the part’s surface. Surface finishes can range from rough to mirror-like, depending on the application.
- Sélection des matériaux: Based on the part’s intended use, engineers choose materials that provide the necessary strength, durability, and machinability.
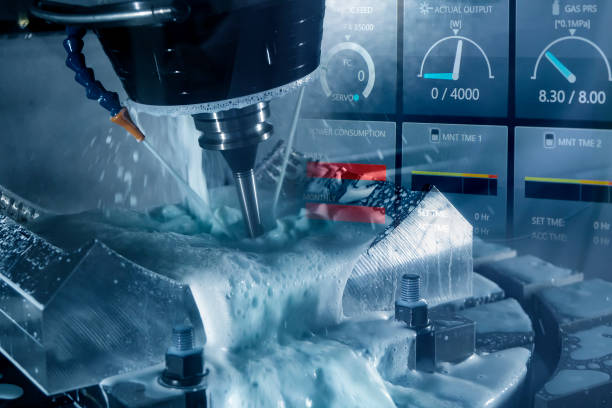
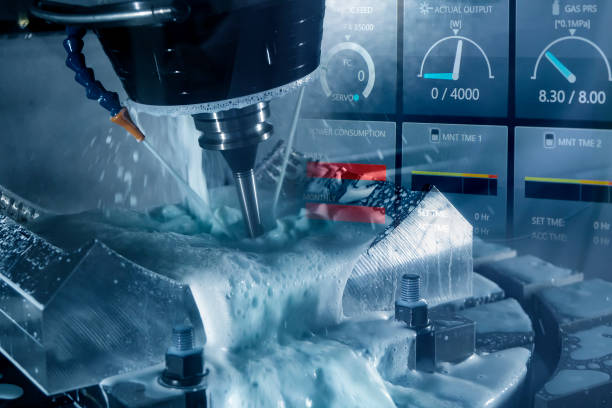
Processus d'usinage
Once the design is finalized, the actual machining process begins. This phase involves several steps to ensure the part is produced accurately and efficiently.
Setup
- Tools: Select the appropriate cutting tools based on the material and design. Common tools include end mills, drill bits, and grinding wheels.
- Machines: Configure CNC machines with the correct tool holders, fixtures, and cutting parameters.
Programmation
- G-Code: The most common CNC programming language, G-code, provides instructions on how to cut the material. It controls the movement of the machine’s axes, spindle speed, feed rate, and tool changes.
- Simulation: Before actual machining, simulations are run to ensure the program will produce the desired part without errors. Simulations help detect potential issues like tool collisions or incorrect tool paths.
Usinage
- Tolérances: Define the acceptable variation in part dimensions. Tight tolerances ensure parts fit together correctly but may increase manufacturing costs.
- Finition de la surface: Specifies the texture and smoothness of the part’s surface. Surface finishes can range from rough to mirror-like, depending on the application.
- Sélection des matériaux: Based on the part’s intended use, engineers choose materials that provide the necessary strength, durability, and machinability.
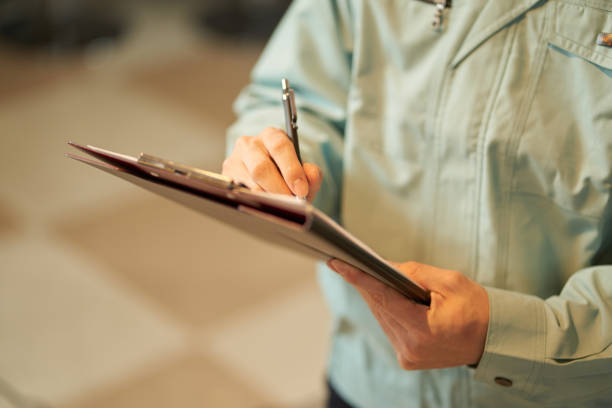
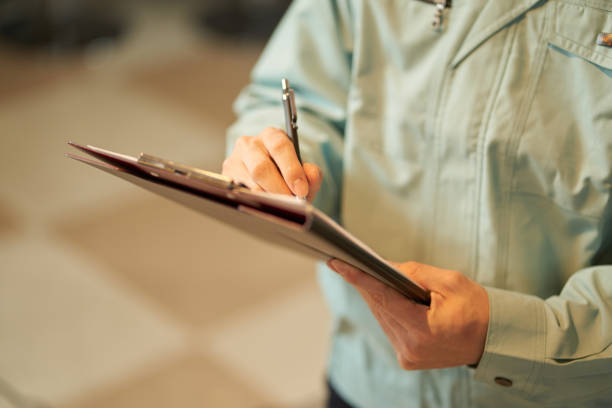
Contrôle de la qualité
Ensuring the parts meet specifications is critical to delivering high-quality products. Quality control involves several inspection methods to verify dimensions, tolerances, and surface finishes.
Inspection Tools
- Calipers and Micrometers: Hand-held tools used for measuring dimensions with high precision. Calipers measure external and internal dimensions, while micrometers provide even finer measurements.
- CMM Machines: Coordinate Measuring Machines (CMM) use a probe to measure the physical geometry of a part. CMMs provide highly accurate measurements of complex shapes and are essential for verifying tolerances.
Process
- Inspection: Parts are inspected at various stages of the machining process. Initial inspections ensure the setup is correct, while final inspections verify the finished part meets all specifications.
- Correction: If deviations are detected, adjustments are made to the machining process or the part is reworked to meet quality standards. Continuous improvement practices are applied to minimize errors and improve overall quality.
Conclusion
Precision machining is a vital manufacturing process that demands skill, precision, and meticulous attention to detail. By understanding the techniques, materials, and quality control measures, you can produce high-quality precision machined parts that meet stringent standards.
In conclusion, precision machining is indispensable in various industries. By following this guide and employing the right tools and techniques, you can create parts that exemplify the highest standards of precision and accuracy.
We are a professional CNC precision machining manufacturer from China. If you have any questions or needs, please feel free to contact us.