¿Qué es el mecanizado CNC?
Computer Numerical Control (Mecanizado CNC) is a manufacturing process where pre-programmed computer software dictates the movement of factory tools and machinery. This process enables the automation of machine tools by means of computers executing pre-programmed sequences of machine control commands. Unlike manual control, which requires live operators to prompt and guide the commands of machining tools, CNC systems operate on a set of programmed instructions without manual intervention.
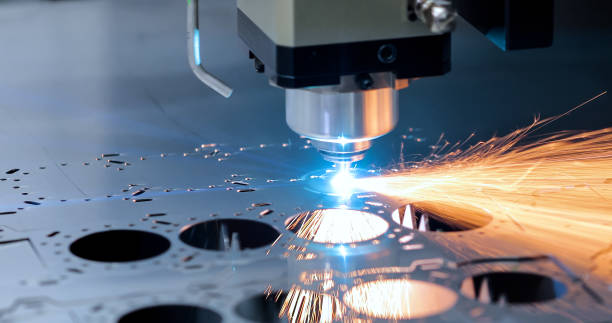
The core of CNC machining is its ability to move and control machine components precisely through software. The desired cuts and movements are programmed into a CNC system, and the corresponding tools perform the tasks without deviation, ensuring high precision and repeatability. This level of automation and precision is achieved through the development and input of detailed computer programming, known as G-code, which directs the machine’s operations such as speed, feed rate, and coordination.
Historically, the evolution of CNC machining began with the use of numerical control (NC) wherein the machine tools were operated via punched tape or cards. With the advent of computers, these systems were enhanced to CNC, providing greater flexibility and control. Modern CNC machines can interpret G-code and execute complex cuts with little to no human intervention, making the process efficient and reducing the margin for error.
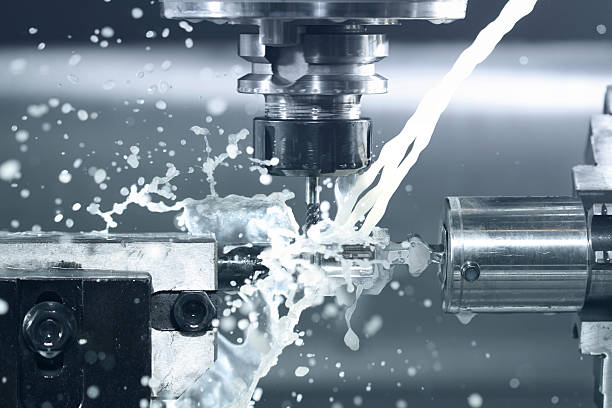
CNC machining technology supports a variety of manufacturing tasks including but not limited to cutting, milling, turning, and drilling of materials ranging from metals and composites to plastics and wood. This versatility makes CNC machining an indispensable part of modern manufacturing, used to produce everything from simple parts to complex components across various industries.
By controlling the machine tools electronically, CNC machining eliminates the need for manual adjustments, thereby enhancing the manufacturing process’s efficiency, accuracy, and safety. This leads to significant improvements in the speed of production and the quality of the finished products, making CNC machining a cornerstone of modern manufacturing.
How CNC Machines Work
Computer Numerical Control (CNC) machining begins with the essential role of a microcomputer that is attached to the machine tool. This computer operates by responding to specific programming languages known as G-code and M-code, which dictate crucial machining parameters like feed rate, spindle speed, cutting tools, and coolant flow. These instructions are then communicated to the machine tool, enabling it to perform tasks without manual intervention, thus ensuring high precision and error-free production regardless of the design complexity.
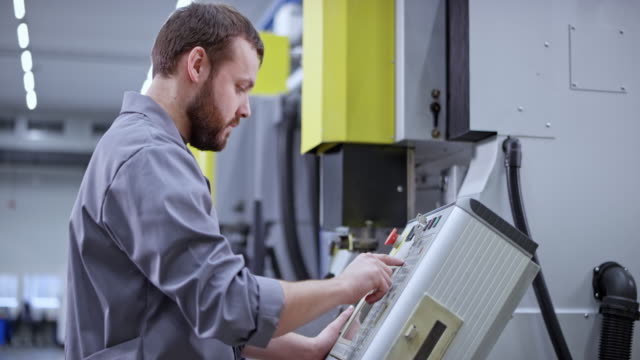
The process of CNC machining is fundamentally subtractive, meaning it involves the removal of material from a workpiece to shape the final product. This is achieved through various machining operations such as turning, drilling, and milling. The instructions for these operations are derived from a CAD model, which is translated into codes that the machine can understand.
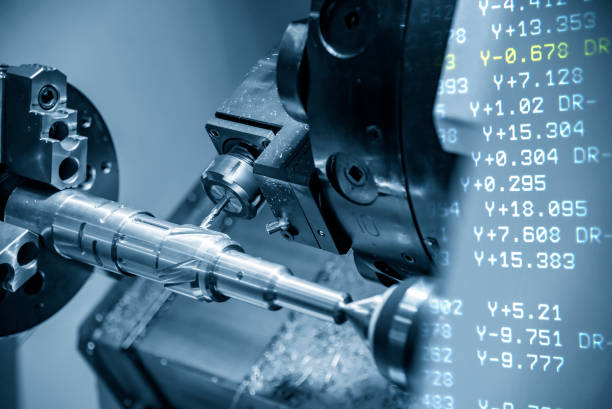
Step-by-Step CNC Machining Process
- Designing the Model: Initially, a 2D or 3D model of the product is created using CAD software like AutoCAD or SolidWorks. This model can be adjusted from 2D to 3D depending on the requirements of the product
- Translating to CNC-Compatible Format:The CAD model is then converted into a CNC-compatible format using CAM software. This conversion is crucial as CNC machines cannot directly interpret CAD models. The CAM software such as AutoCAD and Fusion 360 plays a pivotal role here, ensuring the machine understands all parameters like toolpaths and machine speed.
- Machine and Tool Setup: Before the actual machining starts, the appropriate CNC machine is selected based on the workpiece and product complexity. The workpiece is then securely mounted on the machine. Necessary tools are attached, and machine settings are adjusted to align with the specific requirements of the task.
- Operation and Quality Control: The machining process is fully automated and continues until the program signals completion. Throughout this process, and after its completion, multiple levels of quality inspections are conducted to ensure the product meets all specified standards.
CNC machines are designed to operate with minimal human supervision, primarily relying on the pre-programmed instructions to execute operations. This not only enhances the efficiency of the machining process but also significantly reduces the potential for human error.
In summary, the operation of CNC machines involves a systematic process from design to execution, facilitated by advanced software and precise machine tools. This process ensures efficient production of complex parts with high precision, which is indispensable in modern manufacturing.
Tipos de máquinas CNC
Máquinas CNC de 3 ejes
3-axis CNC machines are the most prevalent type of CNC machining tools. They operate on the X, Y, and Z axes, allowing movement in three directions: left to right, front to back, and top to bottom, respectively. This configuration is ideal for basic machining tasks such as milling slots, drilling holes, and cutting sharp edges on workpieces that do not require complex depth and detailing. Due to their simplicity and effectiveness, 3-axis machines are commonly used in the production of mechanical components and are known for their cost-effectiveness and ease of operation.
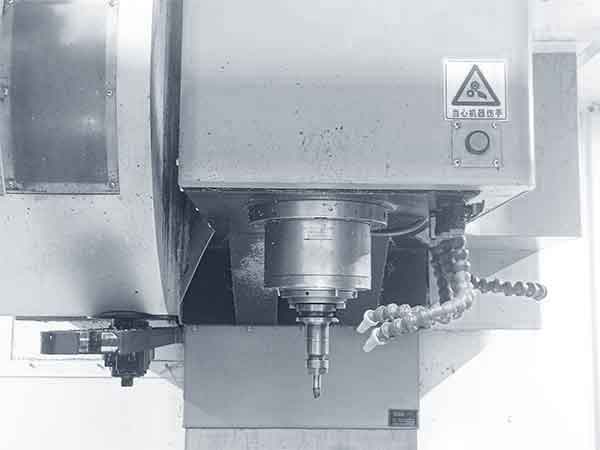
Máquinas CNC de 5 ejes
5-axis CNC machines enhance the capabilities of the traditional 3-axis machines by adding two additional rotational axes, known as the A and B axes, which allow the tool to pivot around the X-axis and rotate around the Y-axis. This configuration enables the machining of complex parts by allowing access to five out of six sides of a workpiece in a single setup. The ability to perform complex cuts with high precision makes 5-axis CNC machines particularly valuable in industries requiring intricate components, such as aerospace and medical technology. These machines are also known for their efficiency, reducing the need for multiple setups and thereby decreasing production time and increasing overall productivity.
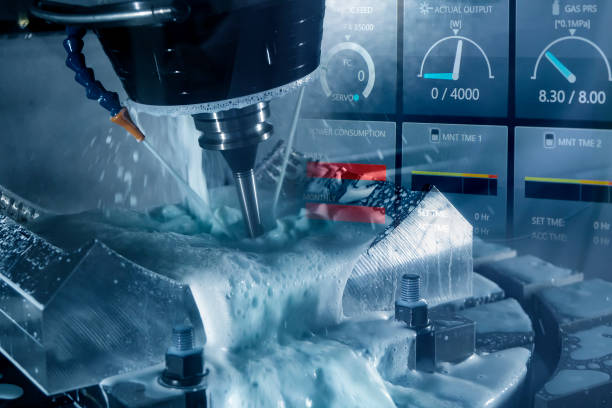
Turning vs Milling Machines
Turning and milling are two distinct CNC machining processes, each suited to different types of materials and production needs. Turning machines, or lathes, work by rotating the workpiece against a stationary cutting tool, primarily used for creating cylindrical components. This method is efficient for quick removal of material from round bar stock.
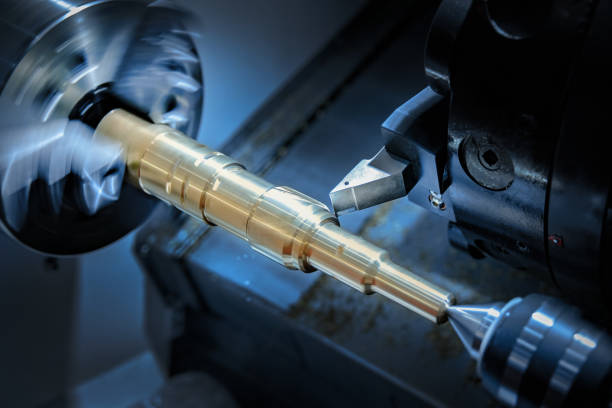
Milling machines, on the other hand, use a rotating cutting tool to remove material from a stationary workpiece. They are better suited for creating flat or irregular surfaces and can handle a wider variety of shapes and materials, including metals and thermoplastics. The versatility of milling machines extends to their ability to work with different cutting tools such as end mills, face mills, and taps, which allows for a broad range of cutting techniques from hollow milling to face milling.
Both turning and milling machines utilize CNC technology for precision and control, ensuring high-quality finishes and accurate parts. However, the choice between turning and milling will depend on the specific requirements of the project, including the complexity of the part and the type of material being used.
Aplicaciones del mecanizado CNC
Industria del automóvil
CNC machining is pivotal in the automotive sector, significantly enhancing the prototyping and manufacturing of complex car components. This technology allows for high precision and repeatability, crucial for parts like engine blocks, gearboxes, and lighting systems. The process is compatible with a diverse range of materials, including metals, plastics, and composites, making it ideal for manufacturing intricate parts that meet tight tolerances. Additionally, CNC machining supports rapid prototyping, enabling automotive engineers to refine designs quickly, which is essential in the competitive automotive market.
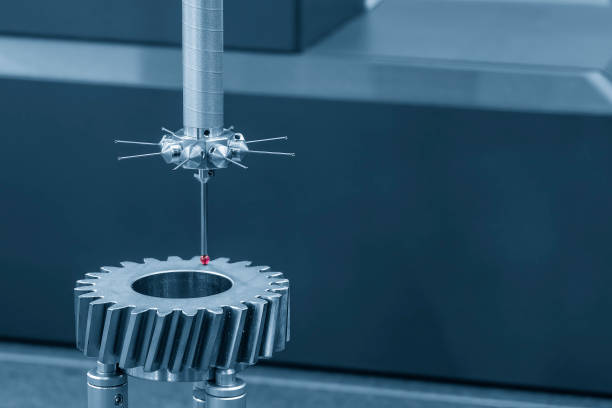
Industria aeroespacial
In the aerospace industry, CNC machining is essential for producing highly precise and critical components such as turbine blades, fuselage parts, and cockpit panels. The technology’s ability to maintain tight tolerances and work with tough materials like titanium and composites aids in manufacturing parts that withstand extreme conditions. Furthermore, the use of 5-axis CNC machines allows for the creation of complex parts that are crucial for the safety and functionality of aircraft and spacecraft.
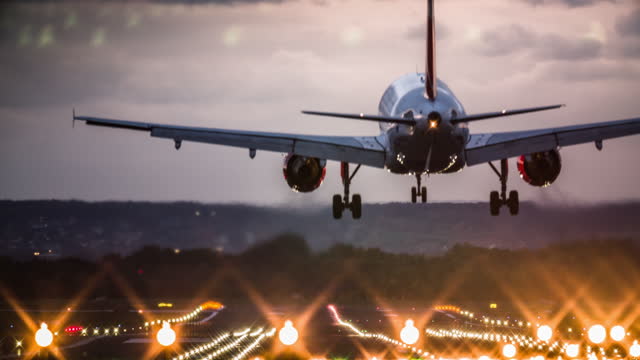
Productos sanitarios
CNC machining’s role in medical manufacturing is critical due to its ability to produce high-grade precision instruments and implants with tight tolerances and excellent surface finishes. This includes surgical tools, orthopedic implants, and components for minimally invasive surgery. The technology ensures the production of devices that are crucial for patient care, such as pacemakers and prosthetic limbs, by enabling customization to patient-specific needs. Moreover, CNC machining is employed in creating microdevices that are essential in various medical applications, including diagnostics and drug delivery systems.
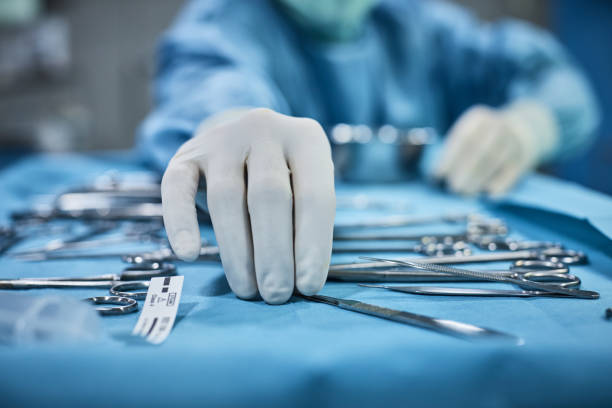
Each of these sectors benefits uniquely from CNC machining, not only in enhancing product quality and safety but also in improving manufacturing efficiency and reducing time-to-market.
Ventajas del mecanizado CNC
Precisión y exactitud
CNC machining is renowned for its precision and accuracy, which are critical in industries where exact specifications are crucial. The process ensures that parts are produced with consistent precision, often achieving tolerances as small as 0.004 mm. This level of detail is essential for applications in aerospace, automotive, and medical industries, where even minor deviations can be unacceptable. The repeatability of CNC machines means that each part is virtually identical, which is vital for large production runs of components that must fit together perfectly in complex assemblies.
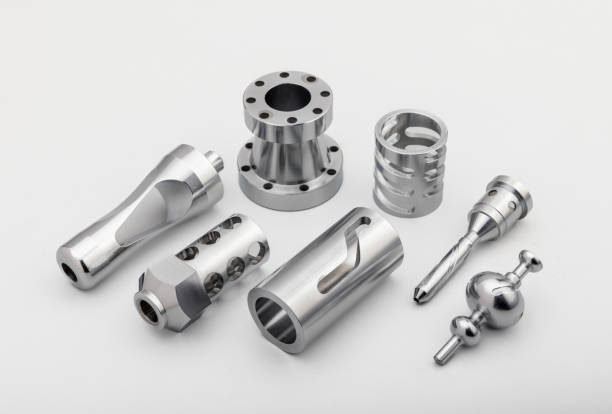
Eficiencia de costes
One of the significant advantages of CNC machining is its cost efficiency. The automation of CNC machines reduces labor costs significantly by minimizing the need for manual intervention, thus not only speeding up the production process but also reducing the possibility of human error. Additionally, CNC machining optimizes material usage, minimizing waste and therefore cost. For instance, companies have reported substantial cost savings by increasing material removal rates and optimizing machining parameters, which in turn enhances energy efficiency. Moreover, the ability to use less expensive materials without compromising the quality further drives down costs.
Escalabilidad
CNC machining offers excellent scalability, making it easier for businesses to increase production without sacrificing quality. The flexibility of CNC machines allows for rapid adjustments to production volumes, adapting quickly to changes in demand. This scalability ensures that manufacturers can respond swiftly to market demands or the need for rapid prototyping, which can be crucial for staying competitive. Additionally, the ability to replicate processes precisely means that scaling up does not lead to a degradation in part quality, which is often a challenge with other manufacturing methods.
By integrating advanced technologies and optimizing production processes, CNC machining not only enhances precision and efficiency but also provides significant cost savings and scalability. This makes it an invaluable process in today’s fast-paced manufacturing environment.
Desafíos en el mecanizado CNC
High Initial Costs
The cost of acquiring CNC machines can be substantial, influenced by factors such as size, complexity, and the specific features required for particular manufacturing tasks. Basic CNC machines might range from $10,000 to $50,000, while more advanced systems could cost up to $500,000 or more. These expenses are further compounded by the costs of installation, training, maintenance, and necessary tooling, which can significantly impact the overall budget.
Complexity in Programming
CNC machining requires precise programming to ensure accurate execution of operations. Errors in programming can lead to significant issues, such as incorrect cutting paths or machine malfunctions. Common errors include inputting incorrect data variables, setup errors, or a lack of understanding of G and M codes, which are critical for the machine’s operation. The programming process involves several steps, from designing a CAD model to converting it into a machine-readable format and finally inputting the G-code into the CNC machine. This complexity necessitates skilled programmers and can be a source of challenges, particularly in intricate or custom designs.
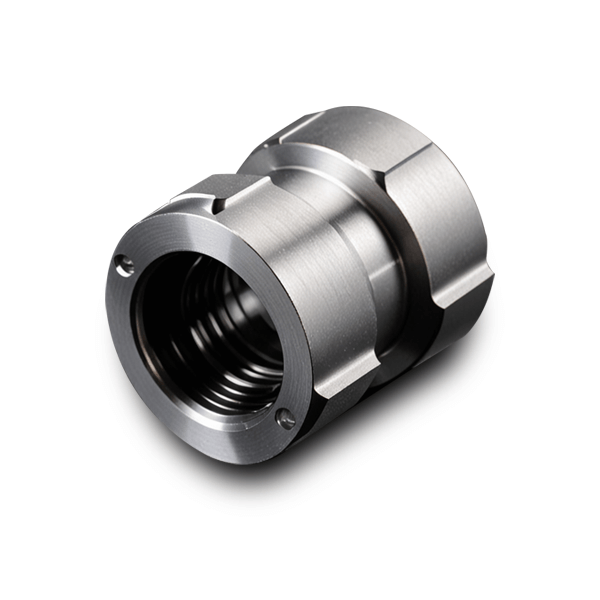
Maintenance Issues
Regular maintenance is crucial for CNC machines to operate effectively. Mechanical systems that are not properly maintained can lead to failures and inaccuracies, affecting the overall productivity and longevity of the machinery. Common maintenance issues include the accumulation of dirt and debris, which can jam moving parts and degrade the machine’s performance. Additionally, environmental factors like temperature can cause overheating, further exacerbating wear and tear. Operators must adhere to a strict maintenance schedule, including regular checks of air filters and cleaning routines, to prevent these issues and ensure the machines function at their optimal level.
Tendencias futuras en el mecanizado CNC
Automation and AI Integration
The integration of artificial intelligence (AI) and automation in CNC machining is set to transform the manufacturing landscape significantly. Innovations in AI, automation, and data analytics are enhancing precision and elevating the efficiency of manufacturing processes. Automation now includes sophisticated robotics that lead to automated tool changes and material handling, significantly enhancing production speed and reducing human error. AI is increasingly playing a crucial role, capable of analyzing large amounts of data to make intelligent decisions that optimize the manufacturing process overall. This includes adapting to varying conditions in real-time to optimize tool paths and prevent tool wear. The future points towards CNC machines that handle more complex processes with greater production speed and efficiency.
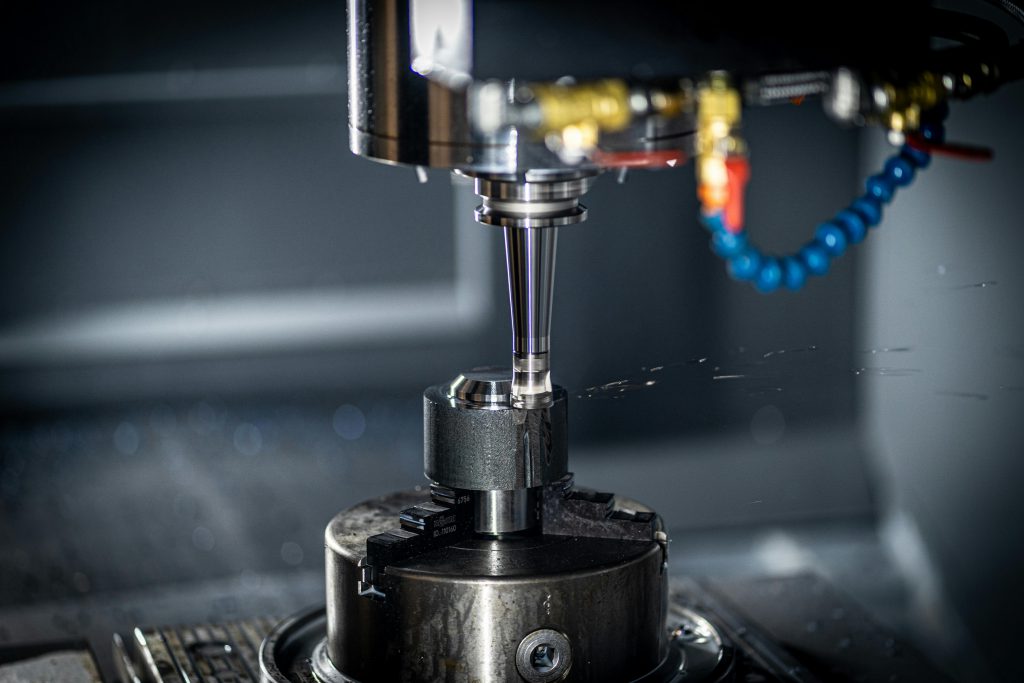
Advancements in Materials
Recent years have seen significant shifts in the materials used in CNC machining. The inclusion of high-performance composites such as carbon fiber reinforced polymers (CFRP) and other fiber-reinforced composites is becoming increasingly popular due to their strength, lightness, and durability. Superalloy metal matrix composites, which are essentially metal alloys in a fiber matrix, exhibit excellent thermal fatigue and corrosion resistance, making them ideal for demanding applications like aerospace parts and naval ship components. These advancements in materials are critical as they enable the creation of more durable and efficient components.
Sustainability Focus
Sustainability is becoming a central focus in CNC machining, with the industry moving towards more eco-friendly practices. The shift to eco-friendly cutting fluids and the selection of sustainable materials for manufacturing are reflections of the industry’s commitment to reducing environmental impact. Innovations such as near-net-shape manufacturing and additive manufacturing are gaining traction because they minimize material usage and waste. Furthermore, the integration of AI and machine learning algorithms optimizes tool paths and enhances overall efficiency, contributing to a more sustainable production environment. Collaborative efforts across the industry are fostering a supportive ecosystem that encourages the adoption of sustainable practices.
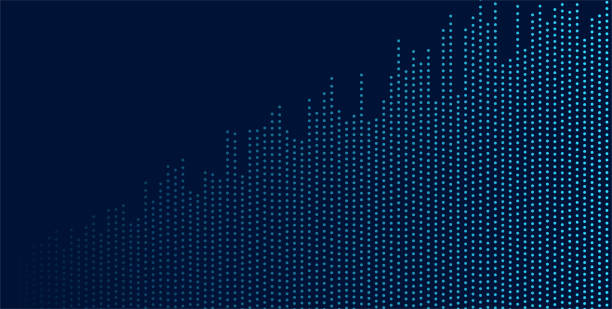
By embracing these future trends, the CNC machining industry is not only enhancing its technological capabilities but is also contributing to more sustainable and efficient manufacturing processes. These advancements promise to redefine the boundaries of what CNC machines can achieve, making them integral to the future of manufacturing.
Conclusión
Throughout this article, we have journeyed through the intricacies of CNC machining, covering its essential concepts, the operational dynamics of CNC machines, the various types available, and their extensive applications across multiple industries. We’ve illuminated the advantages of CNC machining, such as precision, cost-efficiency, and scalability, while also acknowledging the challenges it presents, including high initial costs, complexity in programming, and maintenance issues. The exploration of future trends offered insights into the transformative potential of automation, AI integration, and material advancements, highlighting a steadfast movement towards sustainability and efficiency in manufacturing.
As the manufacturing landscape continues to evolve, CNC machining stands out as a pivotal technology that not only drives innovation but also addresses the pressing need for precision, efficiency, and adaptability in production processes. The integration of advanced technologies and materials, along with a focus on sustainability, underscores the industry’s commitment to improving not only the quality and speed of production but also its impact on the environment. The future of CNC machining is bright, promising to bring about more innovative solutions that will continue to revolutionize manufacturing practices.
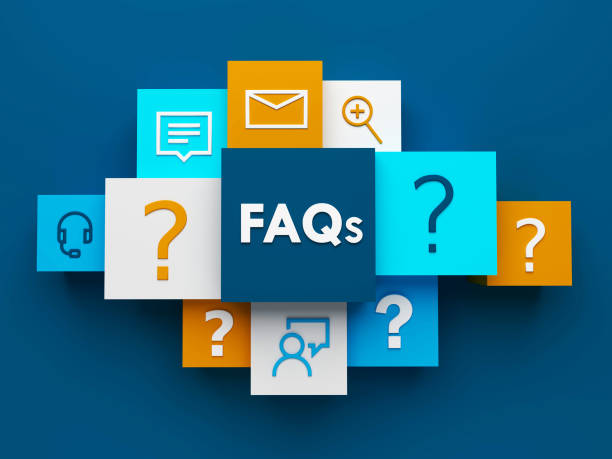
Preguntas frecuentes
1.What are your maximum dimensions for CNC machining??
GCH PROCESS es experto en facilitar la producción y la creación de prototipos de grandes piezas mecanizadas, ya sean de metal o de plástico. Contamos con una amplia superficie de mecanizado CNC de 2000 mm x 1500 mm x 300 mm. Esto garantiza que podamos acomodar incluso piezas de gran tamaño, incluidas las diseñadas para aplicaciones de mobiliario o arquitectura.
2. Can you detail the tolerances of your machined parts??
Por supuesto. La tolerancia exacta que ofrecemos depende de sus requisitos específicos. Para el mecanizado CNC, nuestros componentes metálicos cumplen las normas ISO 2768-m, mientras que nuestras piezas de plástico se ajustan a las normas ISO 2768-c. Cabe señalar que la exigencia de una mayor precisión aumentará en consecuencia el coste.
3. What fundamental knowledge should one have about CNC machines?
CNC, which stands for Computer Numerical Control, involves a manufacturing process that controls a variety of complex functions in machinery. This technology is widely used across industries, particularly in the production of metal and plastic components, where it automates tasks to enhance precision and efficiency.
4. How much does your CNC machining service cost??
The expense associated with our CNC machining service is variable and directly influenced by the distinct attributes of your project, including its design and tolerance specifications. The machining duration for the chosen material is another key determinant of the cost. To illustrate, should you require a part where the combined machining and material expense is $2, with an additional setup charge of $200, the total cost for a singular part would amount to $202. Contrastingly, should you commission the production of 200 identical parts, the cost per unit would be just $3!