In a modern manufacturing facility in aerospace valley, a precisely engineered titanium component takes shape inside a sophisticated Computer Numerical Control (CNC) machine. What once would have taken days of manual machining now emerges with microscopic precision in mere hours. This scene exemplifies how Mecanizado CNC has revolutionized modern manufacturing, enabling unprecedented levels of precision, efficiency, and complexity in part production.
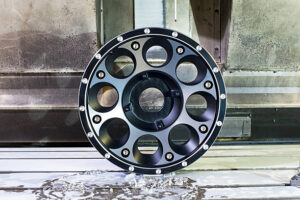
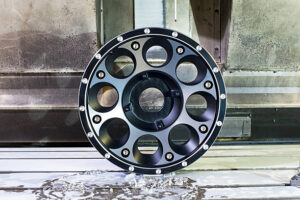
Computer Numerical Control (CNC) machining represents the automation of machine tools through computer programming. Unlike traditional manual machining, where skilled operators control the cutting tools directly, CNC machines follow detailed digital instructions to create complex parts with exceptional accuracy and repeatability.
The journey of CNC technology began in the 1940s and 1950s with the development of Numerical Control (NC) by John T. Parsons. The first commercial NC machines used punched tape for programming. The integration of computer technology in the 1970s marked the birth of modern CNC systems, leading to today’s sophisticated multi-axis machining centers capable of producing incredibly complex components.
The advantages of Mecanizado CNC over traditional methods are substantial. First, it offers unmatched precision, with tolerances as tight as ±0.0001 inches. Second, its automated nature ensures perfect repeatability across production runs. Third, it significantly reduces labor costs while increasing productivity. Finally, CNC enables the creation of complex geometries that would be impossible to achieve through manual machining.
Core CNC Machining Processes
Milling Operations
CNC milling represents one of the most versatile machining processes. Face milling removes material from flat surfaces, while end milling creates various features using rotating cutting tools. Profile milling follows contours to create complex shapes, and slot milling produces channels and grooves.
Modern milling cutters come in various forms. Ball nose end mills excel at creating curved surfaces, while square end mills are ideal for vertical walls and shoulders. Face mills efficiently process large flat surfaces, and specialty cutters handle specific features like T-slots or dovetails.
The success of milling operations depends heavily on proper cutting parameters. Spindle speed (RPM) affects surface finish and tool life, while feed rate determines material removal rate and surface quality. Depth of cut influences cutting forces and machining efficiency. These parameters must be carefully balanced based on the material being cut and the desired outcome.
Turning Operations
CNC turning transforms rotating workpieces by removing material with stationary cutting tools. Basic operations include facing (creating flat ends), turning (reducing diameter), boring (creating internal features), and threading. Advanced turning centers can perform multiple operations simultaneously using several tools.
Turning tools vary based on the operation. External turning tools feature different nose radii and geometries for roughing or finishing. Boring bars reach inside workpieces to create internal features. Thread-cutting tools have specific geometries matched to the desired thread form.
Drilling Operations
While seemingly simple, CNC drilling requires careful attention to detail. Different drill types serve various purposes: twist drills for standard holes, step drills for multiple diameters, and specialized drills for precise tolerances or difficult materials.
Machine Components and Control
The heart of any CNC machine is its spindle system. Modern spindles achieve speeds up to 30,000 RPM or higher, enabling efficient cutting of various materials. Direct-drive spindles offer superior accuracy and longevity compared to belt-driven systems.
Movement control occurs through precise positioning systems along multiple axes. Linear axes (X, Y, Z) handle basic motion, while rotary axes (A, B, C) enable complex 5-axis machining. Advanced feedback systems ensure positioning accuracy within microns.
Materials and Machinability
Material selection significantly impacts machining strategy. Aluminum alloys machine readily at high speeds, making them ideal for rapid production. Steels require more robust cutting tools and slower speeds but offer excellent strength and wear resistance. Titanium presents challenges due to its heat retention and work-hardening properties but is crucial for aerospace applications.
Engineering plastics offer unique advantages in certain applications. ABS and acrylic machine well and provide good dimensional stability. High-performance plastics like PEEK combine excellent machinability with superior mechanical properties.
Programming and Control
Modern CNC programming typically begins with Computer-Aided Manufacturing (CAM) software, which generates toolpaths based on 3D models. These toolpaths are converted to G-code, the standardized programming language for CNC machines. Basic G-code commands control machine movement, spindle speed, feed rate, and tool changes.
Example G-code sequence:
G90 G54 G00 X0 Y0 Z1
G01 Z-0.125 F10
G01 X1 Y1 F20
G00 Z1
Advanced applications increasingly rely on sophisticated toolpath strategies. Trochoidal milling, for instance, maintains consistent tool engagement to extend tool life and increase material removal rates. High-speed machining techniques optimize motion paths to maintain continuous cutter contact.
Industry Applications
CNC machining serves diverse industries with varying requirements. Aerospace demands high-precision components from exotic materials like titanium and Inconel. Medical device manufacturing requires ultra-precise parts from biocompatible materials. Automotive production balances precision with high-volume efficiency.
Safety Considerations
Safe CNC operation requires strict adherence to safety protocols. Essential measures include proper machine guarding, emergency stop systems, and careful handling of cutting tools and materials. Operators must wear appropriate personal protective equipment (PPE) including safety glasses, hearing protection, and steel-toed boots.
Future Developments
The future of CNC machining points toward increased automation and intelligence. Machine learning algorithms are beginning to optimize cutting parameters in real-time. Digital twins enable accurate process simulation and optimization before cutting begins. Integration with additive manufacturing creates hybrid systems capable of both adding and removing material for optimal part production.
Conclusión
CNC machining continues to evolve as a cornerstone of modern manufacturing. Understanding its fundamentals, capabilities, and best practices enables manufacturers to leverage this technology effectively. As automation and digital integration advance, the importance of CNC machining in producing precise, complex components will only grow.
The journey to mastering CNC machining requires continuous learning and adaptation to new technologies. Whether you’re a beginner or an experienced machinist, staying current with evolving capabilities and techniques ensures success in this dynamic field.