The automotive industry is one of the most demanding sectors when it comes to precision engineering and manufacturing. CNC (Computer Numerical Control) machining has become a cornerstone of automotive part production, offering unmatched accuracy, efficiency, and flexibility. In this in-depth guide, we’ll explore how CNC machining automotive parts is transforming the industry, the benefits it offers, and why it’s essential for modern automotive manufacturing.
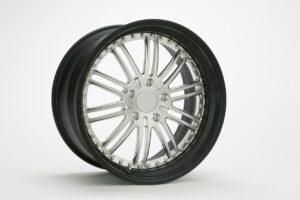
Why CNC Machining is Crucial for Automotive Parts
1. Unmatched Precision
The automotive industry requires components with tight tolerances and complex geometries. CNC machining automotive parts ensures flawless accuracy, down to the micrometer level, which is critical for the performance and safety of vehicles.
2. Material Versatility
CNC machines can work with a wide range of materials, including aluminum, steel, titanium, and high-performance plastics. This versatility allows manufacturers to create durable and lightweight automotive components.
3. High Efficiency
CNC machining automotive parts is highly efficient, enabling the production of large volumes of components in a short time frame. This is especially important in an industry where time-to-market is a critical factor.
4. Cost-Effectiveness
While the initial investment in CNC machines can be high, the long-term cost savings are significant. CNC machining reduces material waste, minimizes errors, and lowers labor costs, making it a cost-effective solution for automotive part production.
5. Customization
The automotive industry is increasingly moving toward customization and personalized designs. CNC machining offers the flexibility to create unique parts tailored to specific requirements.
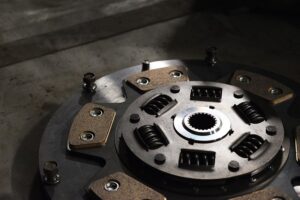
Key Automotive Parts Produced by CNC Machining
1. Engine Components
CNC machining automotive parts such as engine blocks, cylinder heads, pistons, and crankshafts ensures they meet the stringent performance and durability standards required for modern vehicles.
2. Transmission Parts
Gears, shafts, and clutches are critical components of a vehicle’s transmission system. CNC machining ensures these parts are precise and reliable, contributing to smooth and efficient vehicle operation.
3. Brake Systems
Brake calipers, rotors, and pads must be manufactured with extreme precision to ensure safety. CNC machining automotive parts for brake systems guarantees they perform optimally under high stress.
4. Suspension Components
Components like control arms, ball joints, and shock absorbers require high strength and durability. CNC machining ensures these parts can withstand heavy loads and harsh conditions.
5. Interior and Exterior Parts
From dashboard panels to exterior trims, CNC machining automotive parts allows for the creation of aesthetically pleasing and functional components that enhance the vehicle’s design and user experience.
Benefits of CNC Machining Automotive Parts
1. Consistency and Repeatability
CNC machining ensures every part is identical, even in high-volume production runs. This consistency is crucial for maintaining quality standards in the automotive industry.
2. Complex Geometries
CNC machines can produce intricate shapes and designs that are impossible to achieve with traditional manufacturing methods. This capability is essential for modern automotive parts.
3. Reduced Lead Times
The automation and efficiency of CNC machining significantly reduce production lead times, allowing manufacturers to meet tight deadlines and market demands.
4. Improved Durability
CNC machining automotive parts results in components with superior strength and durability, ensuring they can withstand the rigors of daily use and extreme conditions.
5. Sustainability
CNC machining minimizes material waste, making it an environmentally friendly option for automotive part production.
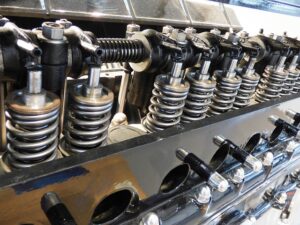
The CNC Machining Process for Automotive Parts
1. Design and Prototyping
The process begins with CAD (Computer-Aided Design) software, where engineers create detailed 3D models of the automotive parts. Prototypes are then machined to test the design and make necessary adjustments.
2. Material Selection
The appropriate material is chosen based on the part’s function and requirements. Common materials include aluminum, stainless steel, and high-performance plastics.
3. CNC Milling
CNC milling is used to create complex shapes and features by removing material from a workpiece. It is ideal for producing engine components, transmission parts, and suspension components.
4. CNC Turning
CNC turning is used for cylindrical parts like shafts and rods. The workpiece rotates while a cutting tool shapes it to the desired dimensions.
5. Finishing Operations
After machining, parts undergo finishing processes such as grinding, polishing, and coating to improve their surface finish and performance.
6. Quality Control
Each part is inspected using advanced measurement tools to ensure it meets the required specifications and tolerances.
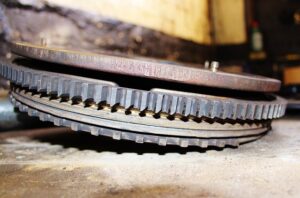
Choosing the Best CNC Machining Partner for Automotive Parts
Selecting the right CNC machining partner is critical for the success of your automotive projects. Here are some factors to consider:
1. Industry Experience
Choose a company with a proven track record in CNC machining automotive parts. Experience in the automotive industry ensures they understand the specific requirements and challenges.
2. Quality Certifications
Ensure the company holds relevant certifications, such as ISO 9001 and IATF 16949, which are specific to the automotive industry.
3. Advanced Technology
The company should use state-of-the-art CNC machines and software to ensure precision and efficiency.
4. Material Expertise
Verify that the company has experience working with the materials required for your automotive parts.
5. Turnaround Time
A reliable partner should offer quick turnaround times without compromising on quality.
6. Customer Support
Good communication and support are essential for a smooth collaboration. Choose a company that is responsive and transparent.
Future Trends in CNC Machining Automotive Parts
1. Electric Vehicles (EVs)
The rise of electric vehicles is driving demand for lightweight and high-performance components. CNC machining automotive parts for EVs requires innovation in materials and designs.
2. Additive Manufacturing Integration
The combination of CNC machining with additive manufacturing (3D printing) is opening up new possibilities for creating complex and lightweight automotive parts.
3. Smart Factories
The adoption of IoT (Internet of Things) and AI (Artificial Intelligence) in manufacturing is transforming CNC machining. Smart factories enable real-time monitoring and optimization of production processes.
4. Sustainable Practices
Automotive manufacturers are increasingly focusing on sustainability. CNC machining companies are adopting eco-friendly practices, such as recycling materials and reducing energy consumption.
5. Customization and Personalization
As consumer demand for customized vehicles grows, CNC machining will play a key role in producing personalized automotive parts.
Case Studies: CNC Machining Automotive Parts in Action
Case Study 1: Electric Vehicle Battery Housings
A leading EV manufacturer partnered with a CNC machining company to produce lightweight aluminum battery housings. The precision and durability of the CNC-machined housings contributed to improved vehicle performance and range.
Case Study 2: High-Performance Engine Components
A racing car manufacturer used CNC machining to create high-performance engine components. The precision and consistency of the machined parts ensured optimal engine performance and reliability.
Case Study 3: Custom Dashboard Panels
A luxury car manufacturer leveraged CNC machining to produce custom dashboard panels with intricate designs. The flexibility of CNC machining allowed for the creation of unique and aesthetically pleasing components.
Category | Details |
Advantages of CNC Machining Automotive Parts | Precision, Material Versatility, High Efficiency, Cost-Effectiveness, Customization |
Key Automotive Parts Produced by CNC Machining | Engine Components, Transmission Parts, Brake Systems, Suspension Components, Interior & Exterior Parts |
The CNC Machining Process for Automotive Parts | Design & Prototyping, Material Selection, CNC Milling, CNC Turning, Finishing Operations, Quality Control |
Choosing the Best CNC Machining Partner | Industry Experience, Quality Certifications, Advanced Technology, Material Expertise, Turnaround Time, Customer Support |
Future Trends in CNC Machining Automotive Parts | Electric Vehicles, Additive Manufacturing, Smart Factories, Sustainable Practices, Customization & Personalization |
Conclusion
CNC machining automotive parts is revolutionizing the automotive industry, offering precision, efficiency, and innovation at every stage of production. From engine components to brake systems and interior parts, CNC machining ensures that every part meets the highest standards of quality and performance.
As the automotive industry continues to evolve, CNC machining will remain at the forefront of manufacturing technology, driving advancements in electric vehicles, sustainability, and customization. By choosing the right CNC machining partner, automotive manufacturers can stay ahead of the competition and deliver superior products to their customers.