Insert Molding Services
Custom insert molding services for high-quality prototypes and on-demand parts. Get quotes at a competitive price and short lead time.
- No minimum order quantities
- Rapid Tooling Production as fast as 2 weeks
- ISO 9001:2015 certificated
- دعم هندسي على مدار 24/7
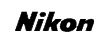
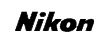
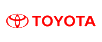
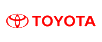
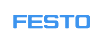
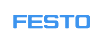
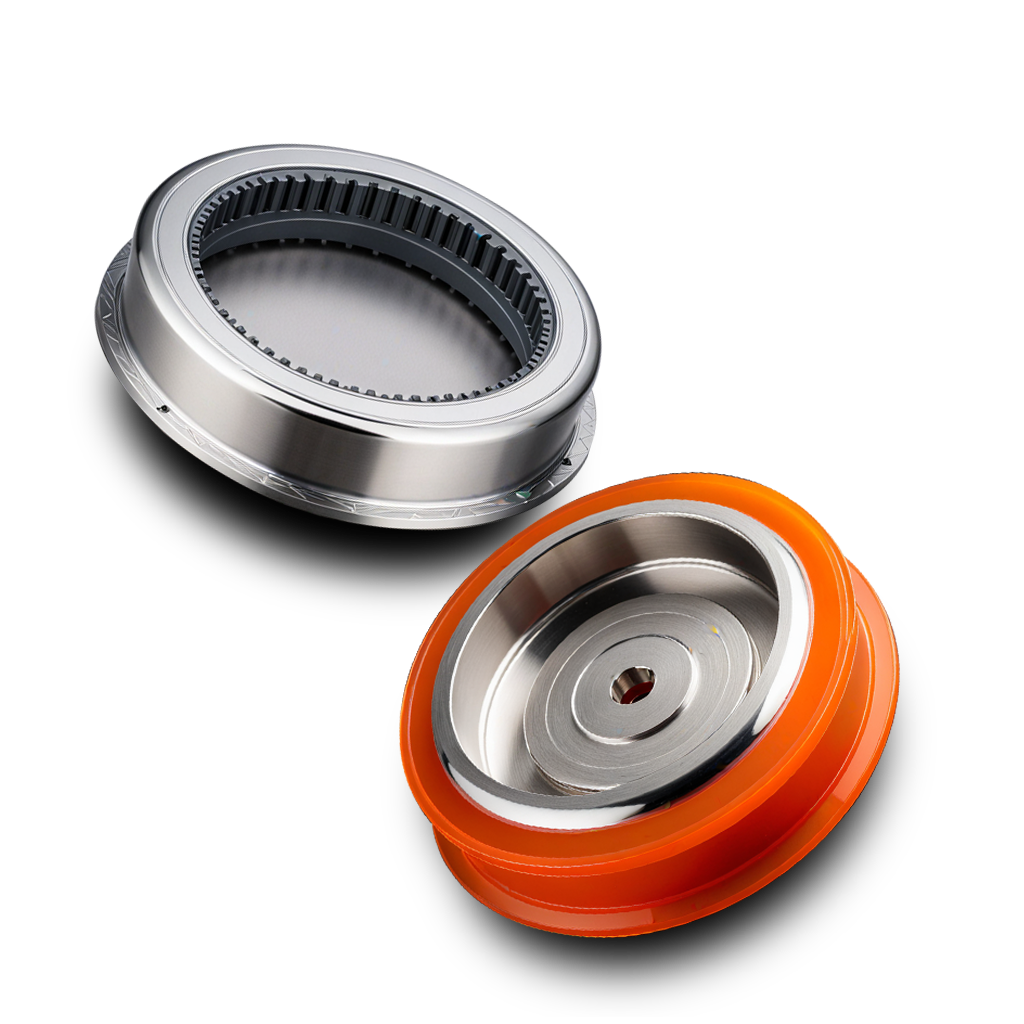
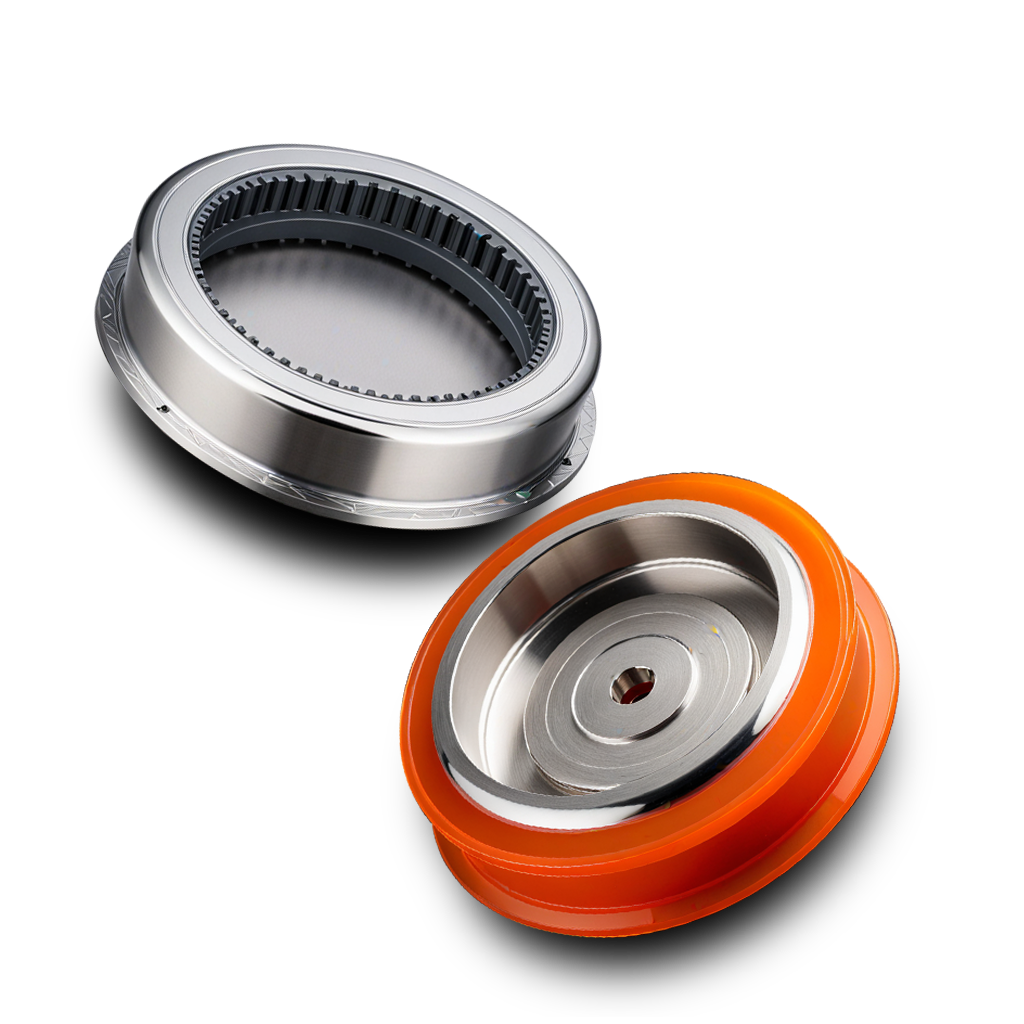
30t-1800t
Instant Quotes
12
تشطيبات السطح
0pc
MOQ
0.025mm
Tolerances
What's Insert Molding
Insert molding is a plastic manufacturing process that involves encapsulating a solid insert with molten plastic. The insert can be made of various materials, such as metal, wood, or another plastic. This method is commonly used when a plastic part requires additional strength, durability, or specific physical properties.


Eliminate assembly: Insert molded parts do not require assembly because there is only one manufacturing process.
Reduce costs: The removal of the assembly process reduces the cost of the insert molding process compared to the standard injection molding.
Reduced part size and weight: Insert molded parts that weigh less than all-metal parts.
Improve part strength: Incorporating plastic and metal inserts increases the durability and strength of the parts compared to other injection molding processes.
Insert Molding from Prototyping to Production
GCH applies strict quality standards to every plastic injection mold, ensuring consistency and quality for molded components. Our experts work with you from prototyping through production to optimize rapid tooling for prototypes and production parts. Every step of our mold production showcases our commitment to quality and customer satisfaction.


Rapid Tooling
Get easy design feedback and validation through superior quality prototype tooling. Create small batches of plastic molded parts with excellent injection molding prototypes. We excel at manufacturing prototype molds within days to ensure you perform functional tests and validate market interest.


Production Tooling
We create high-quality production molds for high-volume plastic parts production. With high-strength, durable tool steel material, our production tooling is suitable for producing hundreds of thousands of parts. We can vary materials and construction methods according to your unique requirements.
GCH Insert Molding Capabilities
GCH’s custom overmolding services ensure the creation of plastic parts that look and perform better. Our production line consists of an overmolding injection molding process that allows us to combine several different materials into one, ensuring you get superior-quality products.
Standards | Metric Units | Imperial Units | |
Maximum Part Size | 800×1000×400mm | 31.50×39.37×15.75in | |
Minimum Part Size | 2×2×2mm | 0.08×0.08×0.08in. | |
Substrate Wall Thickness | From 0.5 to 3mm | From 0.20 to 0.12 in. | |
Tolerance | +/- 0.025 mm | +/- 0.00098 in. | |
Inserts | Inserts can be female and male. They both can improve a product’s appearance and utility. | ||
Mold Validation | Provide T0, T1, T2 samples before mass production | ||
Inspection and Certification Options | First Article Inspection, ISO 9001, ISO 13485 | ||
Lead Time | From mold making to sample delivery: 15-45 business days |
Materials for Insert Molding
We provide a wide range of materials for thermoplastic and inserts that can help you make insert molded parts of different industrial applications. Below are the materials used in custom plastic insert molding and common examples.


Tooling Materials
Before the overmolding process starts low or high-volume production, a high-tolerance CNC machined tooling is needed. Most commonly used materials include:
Tool Steel: P20, H13, S7, NAK80, S136, S136H, 718, 718H, 738
Stainless Steel:
420, NAK80, S136, 316L, 316, 301, 303, 304
Aluminum: 6061, 5052, 7075


الفولاذ المقاوم للصدأ
Plastic injection molding service comes with a wide range of materials with different properties, including impact strength, rigidity, thermal resistance, chemical resistance, etc.
ABS | Nylon (PA) | PC | PVC |
PU | PMMA | PP | PEEK |
PE | HDPE | PS | POM |


Additives and Fibers
Standard plastic materials may not meet custom injection molding parts requirement. In this case, additives and fibers can be added to improve aesthetic and functional properties, providing additional features for your injection molded parts.
UV absorbers | Colorants |
Flame retardants | Glass fibers |
Plasticizers |
Surface Finishes of Insert Molding
Insert molding solutions do not end after cooling and ejection of parts. We also provide a range of surface finishing and post-processing options for the insert molded parts for functional and aesthetic purposes. Common surface finishing options available at GCH for insert molded parts include:
Insert Molding Applications
Plastic insert molding is applicable in making prototypes and full products in several industries. Key industrial applications of insert molding include:
Gallery of Overmolded Parts
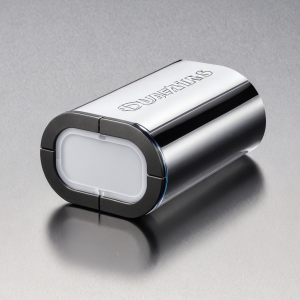
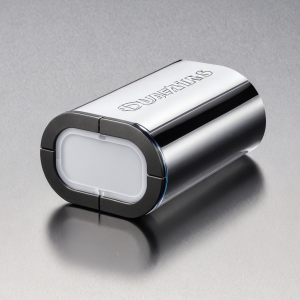
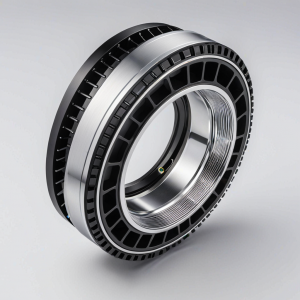
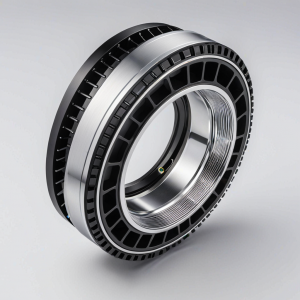
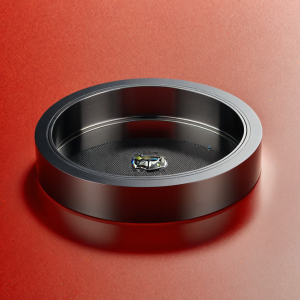
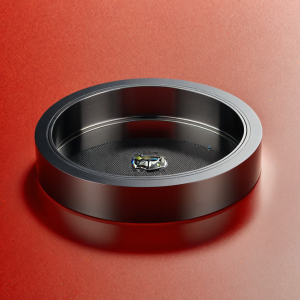
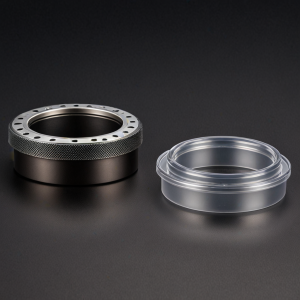
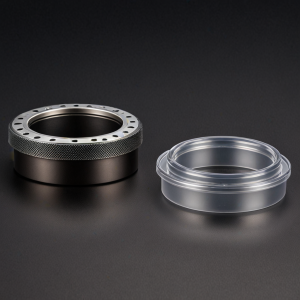
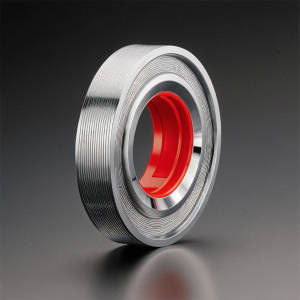
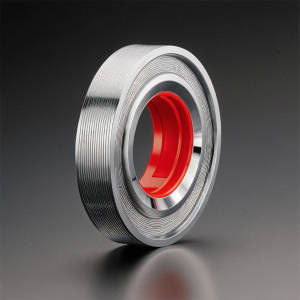
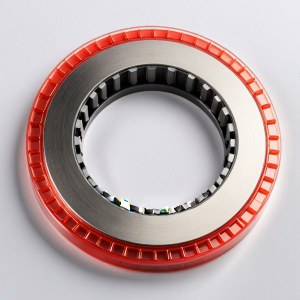
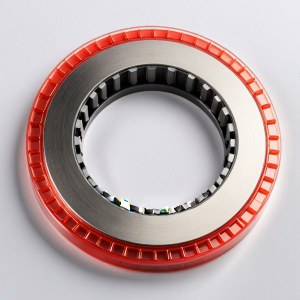
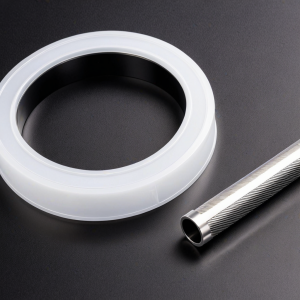
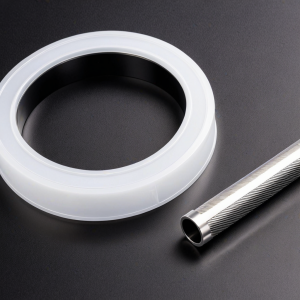


Why Choose GCH
We take an approach that aims to meet your customized needs. We aim to provide long-term prototype overmolding solutions to engineering experts and project managers from design to production. GCH combines cost-effective mold tooling with tech-driven overmolding services that help to make high-quality parts.


No MOQ
No minimum order requirement helps move plastic molded parts from design to production in a fast turnaround and supports your on-demand molding manufacturing needs with reduced injection molding cost.


Tight Tolerance and High Quality
Our plastic injection molding process includes vital design considerations to improve moldability and enhance aesthetic appearance. GCH delivers plastic injection molded parts of varying sizes and complexities. Our standard tolerances are defined by ISO 2768 standards, helping us meet tight tolerance requirements.


High Efficiency
With certified domestic factories and a strong supply chain system, we accelerate the product development cycle and bridge the production of your injection molded parts as fast as possible.


Injection Molding Specialists
Working with our experts having 10+ years of experience in the injection molding industry, efficiently complete a turnaround from prototyping to production.
How Custom Insert Molding Works?
The injection molding process involves feeding raw plastic materials into an injection molding machine, melting them down, and then injecting them into an aluminum or steel mold. Upon cooling, a production-grade thermoplastic part is formed and ejected for further use or assembly.
Gallery of Plastic Injection Molded Parts
Dive into GCH’s extensive gallery that showcases some of our completed injection molded parts and take confidence that we can create your injection molding project according to your strict specifications.
The FAQ
Frequently Asked Questions
Our mold-making process includes 6 steps:
Step 1: Production arrangement: Determine all of the requirements and arrange the production.
Step 2: DFM report analysis: Provide free but detailed production DFM report for further feasibility analysis.
Step 3: Production the mold: Put the mold into production and provide the Tooling Schedule form for the whole cycle for clients to check the process at any time.
Step 4: Free sample to test: Put the mold into production and provide the Tooling Schedule form for the whole cycle for clients to check the process at any time.
Step 5: Mass production:Client confirms the samples are qualified, then officially proceed with the subsequent production.
Step 6: Mold saving: Production is completed and delivered after quality inspection. Mold will be cleaned and properly stored for the next round of parts production.
Tolerances are crucial in injection molding; without proper specification and control, assembly issues can arise. At GCH, we adhere to the ISO 2068-c standard for molding tolerances, but can accommodate tighter specifications if needed.
We have no minimum order requirement. However, larger quantities will yield more competitive pricing.
Once an order is placed, mold design and creation typically take around 35 days, with an additional 3-5 days for the production of the molded parts.
The cost of our services varies based on several factors such as component size, mold complexity, number of cavities, material type, and post-processing requirements. We provide quotes after analyzing these factors on our platform.
At GCH, we offer a wide range of thermoplastic and thermosetting materials suitable for various applications. Some common materials include ABS, Polycarbonate, Polypropylene, and TPE. For a full list of materials or custom material requests, please contact our customer service.
Yes, GCH offers rapid prototyping services. This allows you to test and verify your design before committing to large-scale production.
Latest Posts
فهم التصنيع باستخدام الحاسب الآلي: دليل المبتدئين
خدمات التصنيع الآلي الدقيق باستخدام الحاسب الآلي للقطع المخصصة. حلول عالية الجودة والدقة والكفاءة لمختلف الصناعات.
أفضل المواد المستخدمة في التصنيع باستخدام الحاسب الآلي: دليل شامل
خدمات التصنيع الآلي الدقيق باستخدام الحاسب الآلي للقطع المخصصة عالية الجودة. خبراء التصنيع للتطبيقات الصناعية.
أحدث الاتجاهات في تكنولوجيا التصنيع باستخدام الحاسب الآلي التي يجب أن تعرفها
"مُصنِّع ماكينات دقيقة باستخدام الحاسب الآلي يقدم قطعًا مخصصة عالية الجودة، ونماذج أولية سريعة، وخدمات إنتاجية لتطبيقات الفضاء والسيارات والتطبيقات الطبية والصناعية."