Hey there, fellow engineers! I’ve been working with التصنيع الآلي باستخدام الحاسب الآلي for over two decades now, and I’ve seen firsthand how it’s transformed the manufacturing landscape. Today, I want to break down this powerful technology and give you a clear understanding of its ins and outs.
What is CNC Machining?
In a nutshell, CNC machining, or Computer Numerical Control machining, is a manufacturing process that uses a programmed language to control machine tools for automation. Think of it as a robot with a very specific set of instructions for precisely removing material from a workpiece. It’s a highly versatile and precise method that’s become the backbone of modern manufacturing.
A Blast from the Past: The Origins of CNC
Back in 1949, John T. Parsons and Frank L. Sutlens, working for MIT, laid the groundwork for CNC machining, all thanks to a US Air Force contract for helicopter propeller rotary wings. Initially, this concept, known as Numerical Control (NC), relied on punch cards, making the setup a complex and time-consuming affair. But with the rise of computing power, punch cards became obsolete, and in 1958, the development of G-code brought computer programming into the machining world.
How Does CNC Machining Work?
CNC machining utilizes a programming language that instructs the machine on what to do. Every CNC machine has a built-in computing system called a microcontroller, which interprets these instructions. The program is written using CNC instructions, many of which are standard across different machines. Think of it as a conversation between the programmer and the machine, with the CNC program acting as the language.
The Main Stages of CNC Machining
CNC machining is a multi-step process that typically involves a programmer and an operator. Here’s a breakdown of the essential stages:
- Blueprints and Design: It all starts with creating detailed blueprints, taking into account the part’s features and intended applications. This is usually the domain of designers and engineers.
- CAD Modeling: The blueprint is then transformed into a digital 2D or 3D model using Computer Aided Design (CAD) software. This model provides dimensions, wall thickness, and other vital information.
- CAD to CAM Conversion: CNC machines don’t understand CAD files directly. This is where Computer Aided Manufacturing (CAM) software comes in, converting the CAD data into a machine-readable format.
- Machine Configuration: Before the program executes, the machine needs to be set up. The operator transfers the program to the machine, adjusts settings, mounts the workpiece, and performs necessary checks.
- Program Execution: The operator initiates the program, and the machine starts moving the cutting tools based on the instructions. The program runs until completion or encounters an error.
- Unloading and Inspection: Once the program finishes, the operator removes the workpiece and inspects it for quality. Further processing might be required depending on the application.
Essential Terms in CNC Machining
Navigating the world of CNC requires understanding some key terms:
- Computer Numerical Control (CNC): This is the control system that drives various functions and processes, not just limited to machining.
- Distributed Numerical Control (DNC): DNC connects multiple CNC machines to a central computer system, allowing remote control and monitoring.
- Computer Aided Design (CAD): CAD software creates 2D and 3D drawings, used in various fields beyond machining.
- Computer Aided Manufacturing (CAM): CAM software converts CAD designs into G-code and M-code instructions for CNC machines.
- G-code: These are CNC programming instructions that define the movements of the cutting tools, specifying coordinates, speeds, and actions.
- M-code: M-code instructions control machine-related functions such as coolant flow, program start/stop, tool changes, and more.
- Manufacturing Data Collection (MDC): This system collects feedback data from CNC machines to optimize manufacturing processes and identify bottlenecks.
Types of CNC Machines
CNC machines come in various forms, categorized by their axes of movement and orientation:
Based on Axis:
- 2-Axis CNC: These machines can move in two directions, typically the X and Z axes. Suited for simple cutting and turning operations.
- 3-Axis CNC: The most common type, capable of movement in X, Y, and Z axes. Versatile for various machining processes.
- 4-Axis CNC: Combines the three traditional axes with an additional rotary axis (A, B, or C). Enables machining more complex shapes.
- 5-Axis CNC: Features three traditional axes and two rotary axes, allowing for intricate internal geometries.
- 6-Axis CNC: Combines all six linear and rotary axes, pushing the boundaries of speed and precision.
Based on Orientation:
- Vertical Machining Center: Spindle axis is perpendicular to the work table, offering high precision and a simpler setup.
- Horizontal Machining Center: Spindle axis is parallel to the work table, ideal for smooth surface finishing.
- Universal Machining Center: Combines vertical and horizontal orientations, achieving versatility for multi-sided machining.
Common CNC Machining Operations
Understanding the different machining processes is crucial for applying CNC effectively:
- CNC Drilling: Uses a drill bit to create holes in a workpiece.
- CNC Milling: Employs a stationary workpiece and a rotating cutting tool for precise material removal.
- CNC Turning: Involves a rotating workpiece and a stationary cutting tool, ideal for cylindrical parts.
- CNC Routing: Uses a cutting tool to move across the workpiece, creating intricate shapes and profiles.
- CNC Grinding: A surface finishing process that utilizes abrasive wheels to achieve a smooth finish.
Beyond the Basics:
CNC machining encompasses a wider range of operations, including CNC Broaching, CNC Plasma Cutting, CNC Laser Cutting, CNC Water Jet Cutting, CNC Honing, CNC Lapping, CNC Flame Cutting, and Electrical Discharge Machining (EDM). Each process has its specific applications and capabilities.
Applications of CNC Machining
CNC machining finds its way into various industries, shaping the products we use every day:
- Woodworking: Precision cutting for furniture, intricate carvings, and more.
- Lettering and Engraving: Creating signs, personalized items, and detailed engravings.
- Electronics: Meeting the high precision and consistency demands of electronic appliances.
- Food and Beverage: Hygienic and efficient cutting of food products during packaging.
- Aerospace: Handling the extreme precision and material requirements of aerospace components.
Advantages of CNC Machining
CNC machining offers numerous advantages over traditional manual machining methods:
- Production Speed: CNC machines operate at high speeds, significantly increasing manufacturing output.
- Cost Efficiency: Reduces labor and resource requirements, leading to higher profit margins.
- Consistency: Eliminates human error, ensuring consistent results for mass production.
- Accuracy: CNC machining achieves exceptional accuracy, meeting the stringent demands of industries like aerospace.
- Versatility: Processes a wide range of materials, providing flexibility in manufacturing.
- Lower Rejection Rates: Improved accuracy and consistency lead to fewer defects.
- Data Tracking: Provides data for process optimization and continuous improvement.
Limitations of CNC Machining
While CNC machining has many advantages, it also has some limitations:
- Material Wastage: As a subtractive process, it generates material waste.
- Initial Investment: CNC machines can be expensive to purchase and maintain.
- Operator Skill: Skilled operators are required to maximize the potential of CNC machines.
- Additional Personnel: Requires designers and programmers for program development.
Common CNC Machine Problems
Like any machinery, CNC machines are prone to certain problems:
- Overheating: High heat generated during operation can cause overheating of moving parts.
- Tooling Issues: Incorrect or worn tooling can compromise workpiece quality and machine performance.
- Safety Concerns: Proper safety protocols are crucial to prevent accidents.
Design Tips for CNC Machining
To optimize your designs for CNC machining, follow these tips:
- Simulations: Run simulations to identify potential issues before machining.
- سُمك الجدار: Ensure adequate wall thickness to prevent breakage.
- Tool Path and Offsets: Consider tool path movement and offsets for efficient machining.
The Future of CNC Machining
CNC machining is continuously evolving, embracing Industry 4.0 concepts:
- Remote Control and Automation: Intelligent systems enable remote operation and automation.
- Data-Driven Optimization: Data collection and analysis drive process optimization and continuous improvement.
- Miniaturization: CNC machining is being used for smaller parts, including semiconductor wafers.
- Robotic Integration: Robotic arms integrated with CNC machines automate machining processes.
More expertise:
What is CNC Machining: Definition, Operations, Machines & Applications
Our Insights
CNC machining is a game-changer for manufacturing, pushing the boundaries of precision and efficiency. It’s a testament to human ingenuity and a force shaping the products we use every day. As technology continues to advance, CNC machining will undoubtedly become even more sophisticated and integral to the future of manufacturing.
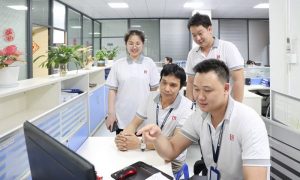
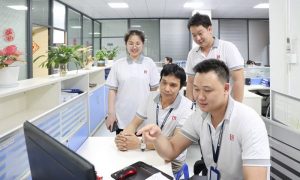
Remember, my friend, if you’re looking for reliable, high-quality, and cost-effective manufacturing solutions, GCH PROCESS is definitely worth considering.