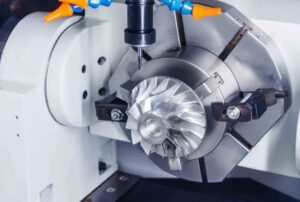
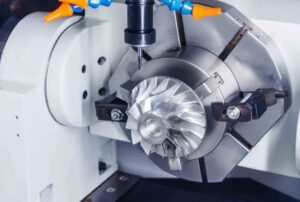
What is 5-Axis CNC Machining?
To understand 5-axis CNC machining, let’s break it down. CNC stands for Computer Numerical Control, a digital system that automates machine tools. Typical CNC machines operate on three axes: X (vertical), Y (horizontal), and Z (up and down). Adding two more axes (A, B, or C) allows 5-axis machines to perform more complex movements and create parts with intricate geometries and superior surface finishes. This advanced capability makes 5-axis CNC machining ideal for manufacturing complex components efficiently.
Differences Between 3-Axis, 4-Axis, and 5-Axis CNC Machining
3-Axis CNC Machining: The most common type, 3-axis CNC milling involves the movement of the cutting tool along the X, Y, and Z axes. It’s suitable for parts with cubic geometries but requires manual repositioning for complex shapes. It’s cost-effective for simpler tasks but limited in handling intricate designs.
4-Axis CNC Machining: This adds an A-axis (rotation around the X-axis) to the 3-axis setup, enabling more versatile machining without multiple setups. It improves efficiency and accuracy for parts needing machining on multiple sides.
5-Axis CNC Machining: This technology allows simultaneous movement along the X, Y, and Z axes, and rotation around two additional axes (A, B, or C). It can machine five sides of a part in one setup, ideal for complex geometries and deep cavities. There are two main types: indexed 3+2-axis and continuous (full) 5-axis. While indexed 3+2-axis rotates axes independently, continuous 5-axis machining allows simultaneous movement, producing highly complex parts with tight tolerances.
Applications of 5-Axis CNC Machining
5-axis CNC machining is pivotal for industries requiring intricate and high-precision components:
- Medical Industry: It produces precise medical devices, implants, and healthcare equipment.
- الطيران والفضاء: It manufactures parts with smooth shapes and contoured edges, crucial for lightweight and durable aerospace components.
- Military: It creates components for precise military equipment, including engine parts and sensors.
CNC Machining Tools
CNC milling utilizes various cutting tools to shape parts:
- Drill Bit: For creating holes with circular cross-sections.
- Twist Drill: A rod with helical flutes for drilling.
- End Mill: For shaping and drilling during milling.
- Face Mill: A tool with carbide inserts for making flat surfaces.
- Hollow Mill: Used in screw machines for roughing and finishing.
- Thread Mill: For cutting and making threads.
- Slab Mill: Removes large amounts of material.
- Gear Cutter: Creates gears through milling, hobbing, and other processes.
- Fly Cutter: A single-point rotary tool for large flat surfaces.
- Reamer: Enlarges or finishes drilled holes with high precision.
CNC Machining Centers
CNC machining centers perform operations like drilling, milling, and turning with high precision. Types include:
- Horizontal Machining Center: With a horizontal spindle and automatic tool changer (ATC), suitable for high-volume production.
- Vertical Machining Center: Ideal for surface engraving, typically with three axes.
- Universal Machining Center: Combines horizontal and vertical capabilities with continuous spindle tilting.
Cost of 5-Axis CNC Machines
The cost of 5-axis CNC machines varies significantly based on type and features, ranging from $10,000 to $500,000. Indexed 3+2 machines typically cost between $35,000 and $200,000, while high-end full 5-axis machines range from $150,000 to $500,000. Desktop models start around $10,000. Manufacturers like GCH offer customized solutions to meet specific needs.
Advantages of 5-Axis CNC Machining
- Improved Quality and Efficiency: Enhanced cutting tool tangential movement reduces cycle times and costs.
- Better Cutting Conditions: Maintains optimal conditions by rotating the table, achieving superior surface quality.
- Reduced Fixture Use: Minimizes additional fixtures, cutting costs and maintenance.
- Streamlined Production: Shortens the process chain, simplifying management and scheduling.
- Advanced Technology: 5-axis machining offers unmatched efficiency and quality, ensuring a competitive edge.
In conclusion, 5-axis CNC machining is a powerful technology that enhances the production of complex parts. Choosing the right method—whether 3-axis, 4-axis, or 5-axis—depends on your specific requirements, including material, volume, budget, and complexity. For intricate designs and tight tolerances, 5-axis machining provides a superior solution.