Introduction
CNC (Computer Numerical Control) machining has revolutionized the manufacturing landscape, becoming a cornerstone of precision engineering. This advanced technology allows manufacturers to create intricate components with unmatched accuracy and repeatability. CNC machining manufacturers are pivotal to various sectors, including aerospace, automotive, medical, and electronics, where precision is paramount. This article delves into the intricacies of CNC machining, the role of manufacturers, and the myriad benefits they provide, expanding to cover industry applications, technological advancements, and future trends.
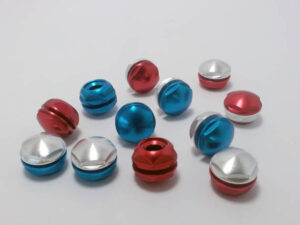
What is CNC Machining?
CNC machining is a subtractive manufacturing process that utilizes computer-controlled machines to remove material from a solid block, or workpiece, to create the desired part. This process is characterized by its ability to produce highly complex geometries and tight tolerances, often within a few microns.
The CNC Machining Process
- Design Phase: The process begins with a Computer-Aided Design (CAD) model of the part. Engineers create a detailed 3D model using CAD software, which includes dimensions, tolerances, and material specifications.
- Programming: Once the design is finalized, it is converted into a Computer-Aided Manufacturing (CAM) program. This program generates the tool paths that the CNC machine will follow. The programmer considers factors such as cutting speeds, feed rates, and tool selection during this phase.
- Machining: The CAM program is uploaded to the CNC machine, which begins the machining process. The machine uses various tools to cut, mill, drill, or turn the material according to the programmed instructions.
- Quality Control: After machining, the parts undergo rigorous quality inspection. This may include measurements using coordinate measuring machines (CMM) or other precision instruments to ensure they meet specified tolerances.
- Finishing: Finally, additional processes like polishing, anodizing, or coating may be applied to enhance the surface finish or add specific properties to the part.
The Role of CNC Machining Manufacturers
CNC machining manufacturers are specialized firms that provide precision machining services tailored to the needs of their clients. Their responsibilities encompass a wide range of activities:
Custom Part Production
One of the primary functions of CNC machining manufacturers is the production of custom parts. Clients often provide specifications for unique components that must meet specific performance requirements. Manufacturers utilize their expertise to produce these parts, ensuring adherence to quality and precision standards.
Prototype Development
Manufacturers frequently assist in the creation of prototypes for new products. Prototyping is a critical step in the product development process, allowing designers and engineers to test and validate their ideas before committing to full-scale production. CNC machining enables rapid prototyping, significantly reducing the time from concept to market.
Mass Production
For businesses requiring large quantities of components, CNC machining manufacturers can efficiently scale production. This capability is essential in industries like automotive and electronics, where high-volume production is necessary to meet market demand. The ability to produce consistent, identical parts ensures that companies can maintain their production schedules without compromising quality.
Material Sourcing
Many CNC machining manufacturers also offer material sourcing services. They have established relationships with suppliers and can assist clients in selecting the most suitable materials for their projects. This service not only saves time for clients but also ensures that the materials chosen align with the required specifications, performance characteristics, and budget.
Benefits of CNC Machining
CNC machining offers numerous advantages that make it a preferred choice for manufacturers across various industries:
1. Precision and Accuracy
CNC machines are capable of achieving tolerances as low as a few microns. This level of precision is crucial in industries where even the slightest deviation can lead to product failure. The automated nature of CNC machining minimizes human error, resulting in consistently accurate components.
2. Consistency
Once a CNC machine is programmed, it can produce thousands of identical parts with minimal variation. This consistency is vital for mass production, allowing manufacturers to meet tight deadlines and maintain quality assurance.
3. Complex Geometry
CNC machining can create intricate designs and complex geometries that would be challenging or impossible to achieve with traditional machining methods. This capability opens up new possibilities for product design and innovation.
4. Reduced Lead Times
The automation of CNC machining significantly speeds up the production process. With the ability to run machines unattended, manufacturers can operate around the clock, reducing lead times and increasing overall efficiency.
5. Cost-Effectiveness
While the initial setup costs for CNC machining may be higher than traditional methods, the long-term benefits often outweigh these costs. Reduced waste, lower labor costs, and increased production efficiency lead to significant cost savings over time.
Industries Served
CNC machining manufacturers serve a diverse range of industries, each with its unique requirements and challenges:
Aerospace
The aerospace industry demands the highest levels of precision and reliability. CNC machining manufacturers produce critical components for aircraft and spacecraft, including engine parts, structural components, and control systems. These parts must adhere to stringent safety and performance standards, making CNC machining essential for this sector.
Automotive
In the automotive industry, CNC machining is used to manufacture a wide variety of components, from engine blocks to transmission parts. The ability to produce high volumes of precise components quickly is vital in this competitive market. CNC machining also allows for rapid prototyping of new automotive designs, reducing the time to market for new vehicles.
Medical Devices
Medical device manufacturing is another sector that relies heavily on CNC machining. Components used in surgical instruments, implants, and diagnostic equipment require exceptional precision and reliability. CNC machining enables manufacturers to create these complex parts while maintaining strict adherence to regulatory standards.
Electronics
The electronics industry utilizes CNC machining for producing housings, printed circuit boards (PCBs), and other intricate components. As devices become smaller and more complex, the demand for precision-machined parts continues to grow.
Technological Advancements in CNC Machining
As technology continues to evolve, CNC machining manufacturers are adopting new innovations to enhance their capabilities:
1. Advanced Materials
The development of new materials, such as composites and advanced alloys, has expanded the possibilities for CNC machining. Manufacturers can now work with materials that offer superior strength-to-weight ratios and enhanced performance characteristics.
2. Automation and Robotics
The integration of automation and robotics in CNC machining processes is transforming the industry. Automated systems can manage loading and unloading parts, reducing labor costs and increasing throughput. Robotics can also perform tasks such as quality inspection, further enhancing efficiency.
3. IoT and Smart Manufacturing
The Internet of Things (IoT) is making its way into CNC machining, allowing manufacturers to monitor machine performance in real-time. Smart manufacturing systems can analyze data from machines to identify inefficiencies, predict maintenance needs, and optimize production schedules.
4. Additive Manufacturing Integration
Some CNC machining manufacturers are exploring the integration of additive manufacturing (3D printing) with traditional machining processes. This hybrid approach allows for the rapid production of complex geometries while still utilizing CNC machining for finishing and precision.
Future Trends in CNC Machining
As the manufacturing landscape continues to evolve, several trends are likely to shape the future of CNC machining:
1. Increased Customization
With the rise of consumer demand for personalized products, CNC machining manufacturers will need to adapt to provide more customized solutions. This trend may drive the development of more flexible and agile manufacturing processes that can quickly respond to changing customer needs.
2. Sustainability
Sustainability is becoming a critical consideration for manufacturers across all industries. CNC machining manufacturers will need to focus on reducing waste, optimizing material usage, and adopting eco-friendly practices to meet regulatory requirements and consumer expectations.
3. Workforce Development
As technology advances, the demand for skilled workers in CNC machining will continue to rise. Manufacturers will need to invest in workforce development programs to ensure that employees have the necessary skills to operate advanced machinery and understand complex processes.
4. Globalization and Supply Chain Optimization
Globalization will continue to impact CNC machining manufacturers, requiring them to optimize their supply chains and production processes. Companies may need to establish strategic partnerships with suppliers and customers worldwide to remain competitive.
Conclusion
CNC machining manufacturers are essential players in the modern manufacturing landscape, providing the precision and efficiency needed to meet the demands of various industries. Their ability to produce high-quality, complex components rapidly makes them invaluable to sectors such as aerospace, automotive, medical devices, and electronics. As technology continues to advance, CNC machining will likely play an even more significant role in shaping the future of manufacturing, driving innovation, and improving product quality. For businesses looking to enhance their production capabilities and stay competitive, partnering with a reliable CNC machining manufacturer is a strategic move that can lead to long-term success.