Laser Cutting Service
- Lead time as fast as 3-5 days
- ISO 9001:2015 certificated
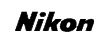
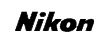
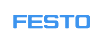
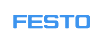
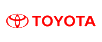
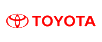
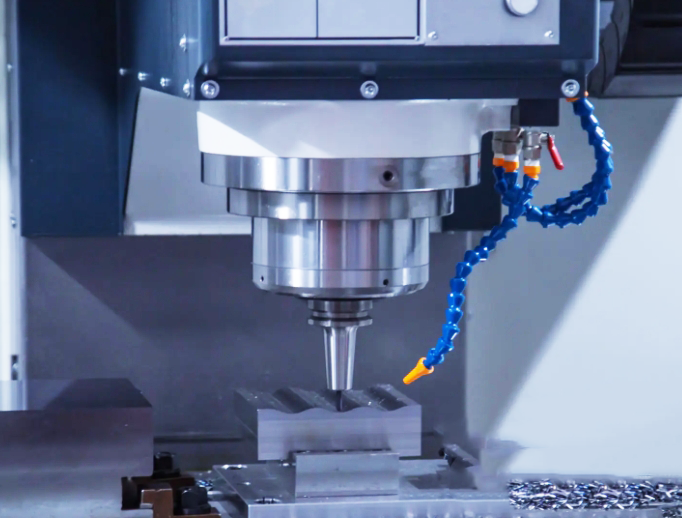
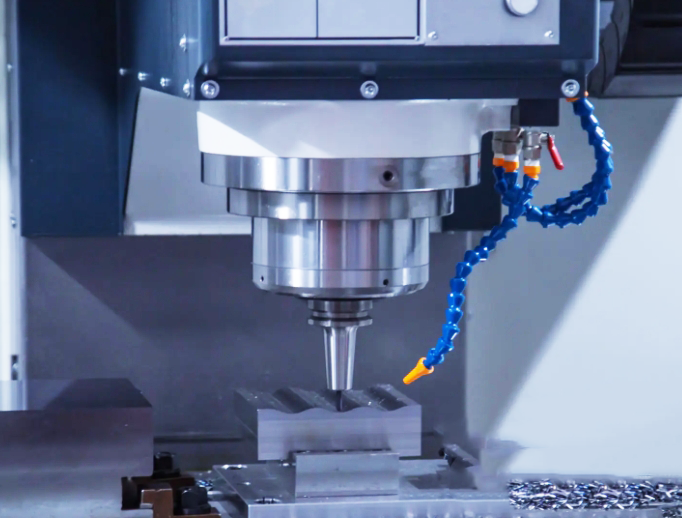
30t-1800t
Instant Quotes
12
Surface Finishes
0pc
MOQ
0.025mm
Tolerances
What Is Plasma Cutting?
Plasma cutting is a production process involving the use of ionized gas at temperatures above 20,0000C to melt and remove material from a workpiece. The gasses used here include argon/hydrogen, argon, or nitrogen. Plasma cutting is ideal for making high-precision parts with both general and industry-specific applications. You could get numerous benefits from using GCH’s custom plasma cutting service when making your product parts. Some of these advantages include:


- High Precision and Repeatability: Precision and repeatability are one of the major strengths of our plasma-cutting service. This is especially true when cutting shapes and angles from a metal workpiece. At GCH, we boast experienced operators with steady hands that guarantee a clean, highly precise cut.
- Versatility to Various Materials: Versatility is one of the major advantages of fabricating metals using plasma cutting. This is due to its ability to cut through conductive metals like iron, copper, stainless steel, steel, brass, and other metals. Besides, plasma cutting has one of the fastest cutting speeds, making it one of the best methods for metalwork.
- Suitable for Different Thickness: Unlike other metal cutting options, CNC plasma cutting can cut metals with various thicknesses. Our plasma cutting team at GCH can cut metals with thicknesses up to one-and-half inch and thicker.
- Complex Shapes: Plasma cutting facilitates the creation of various shapes, regardless of the complexity of their geometry. At GCH, we use plasma cutting to create intricate shapes, straight lines, and curves that would be impossible to make using other metal-cutting techniques.
- Energy Efficient: Energy efficiency is one of the reasons why more companies and businesses are leaning towards plasma cutting. At GCH, our CNC plasma machines are energy efficient, saving the long run cost.
Laser Cutting From Prototyping to Production
The versatility and precision of laser cutting ensure excellent initial product development and continuous production. Design files are rapidly turned into end products, from intricate custom parts to complex enclosures.


Functional Prototype
Create prototypes with intricate details and fine features that might be difficult to achieve using other cutting methods. Allowing for quick turnaround times and reducing the overall production time.


Rapid Prototyping
Create quick and precise cuts for a variety of materials. This can include creating test pieces, evaluating designs, and producing small quantities of a product for testing and validation.
GCH Overmolding Capabilities
GCH’s custom overmolding services ensure the creation of plastic parts that look and perform better. Our production line consists of an overmolding injection molding process that allows us to combine several different materials into one, ensuring you get superior-quality products.
Standards | Description |
Thickness | Aluminum≤40 mm, Steel≤50 mm, Stainless Steel≤50 mm |
Cutting Tolerance | The standard tolerance level for plasma cutting ranges between 0.1 to 0.2mm. This tolerance level depends majorly on the size of the part and general requirements. However, at GCH, we adjust our tolerance levels to match our customer’s requirements. |
Cutting Area | The cutting area for thin sheet aluminum of up to 4mm thickness is 1000 x 2000mm, 1250 x 2500 mm, and 1500 x 3000mm. While cutting area for thick sheets of steel over 4mm thickness is 1500 x 3000mm, 2000 x 3000mm, 1500 x 6000mm |
Lead time | 5 days or more |
Kerf (slit size) | About 0.5 mm (0.02 in.) |
Edge condition | Laser cut edges have matte and vertical lines. |
Laser sources | CO2 and fiber lasers. Up to 10 kW. |
Repeatability | +/- 0.05 mm (0.002 in.) |
Positioning accuracy | +/- 0.10 mm (0.004 in.) |
Lead Time | 5-7 days |
Materials for Plasma Cutting
GCH’s laser cutting service is versatile and compatible with various materials, ranging from ferrous to non-ferrous metals, plastics, and other non-metals. Our laser cutting facility combines ultra-modern technology with skilled professionals to laser cut materials across different strengths, weights, and thermal properties. Here are some laser cutting materials available for your project.


Aluminum
Aluminum’s ability to reflect heat is one of the reasons why machinists favor this metal as a plasma-cutting material. It is also lightweight, non-corrosive, and highly malleable. Furthermore, aluminum is cost-effective, with a shorter plasma cutting time compared to other materials. Aluminum also has a high rate of recyclability, which helps reduce waste in the long term.
Subtypes: 2024, 5052, 5083, 6061, 6063, 6082, 7075


Steel
Steel is one of the most popular metals in machine shops due to its high machinability. Asides from machinability, steel has high tensile strength, ductility, and malleability. It is also very durable, with an aesthetically pleasing appearance. One major reason steel is ideal for plasma cutting is its high weldability, which allows it to withstand the stress caused by heat from the plasma cutter.
Subtypes: 1018, 1020, 1025, 1045, 1215, 4130, 4140, 4340, 5140,A36,ST37


Stainless Steel
Stainless steel is a metal alloy that contains at least 11% chromium. The chromium content of this metal gives it a glossy appearance. This metal is ideal for plasma cutting due to its strength at high temperatures, as it performs better than most metals. Stainless steel also has a high tensile strength and good plasticity. Besides, stainless steel is quite easy to machine.
Subtypes: 201, 303, 304, 316, 316L, 420, 430, 431, 304
Finishing Options for Plasma Cutting
Parts made using plasma cutting usually feature excellent finishes. At GCH, we offer various custom finishing options that boost the produced part’s functionality, appearance, and durability.
Name | Materials | Color | Texture | Thickness | |
![]() ![]() | Anodizing | Aluminum | Clear, black, grey, red, blue, gold. | Smooth, matte finish. | A thin layer: 5-20 µm Hard anodic oxide film: 60-200 µm |
![]() ![]() | Beed Blasting | ABS, Aluminum, Brass, Stainless Steel, Steel | N/A | Matte | 0.3mm-6mm |
![]() ![]() | Powder Coating | Aluminum, Stainless Steel, Steel | Black, any RAL code or Pantone number | Gloss or semi-gloss | 5052 Aluminum 0.063″-0.500” 6061 Aluminum 0.063″-0.500” 7075 Aluminum 0.125”-0.250″ Mild Steel 0.048″-0.500” 4130 Chromoly Steel 0.050″-0.250” Stainless Steel 0.048″-0.500” |
![]() ![]() | Electroplating | Aluminum, steel, stainless steel | N/A | Smooth, glossy finish | 30-500 µin |
![]() ![]() | Polishing | Aluminum, Brass, Stainless Steel, Steel | N/A | Glossy | N/A |
![]() ![]() | Brushing | Aluminum, Brass, Stainless Steel, Steel | Varies | Satin | N/A |
![]() ![]() | Silkscreen Printing | Aluminum, Brass, Stainless Steel, Steel | Varies | N/A | < 1 µm |
![]() ![]() | Passivation | Stainless Steel | None | Unchanged | 5μm – 25μm |
Gallery of Plasma Cut Parts
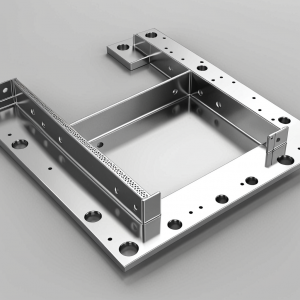
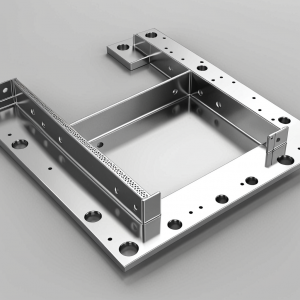
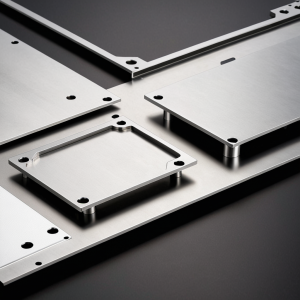
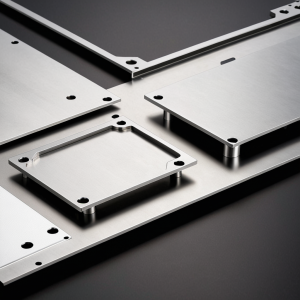
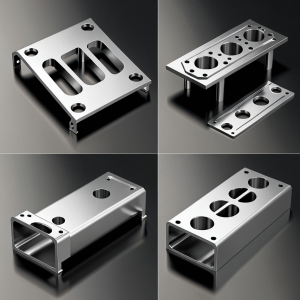
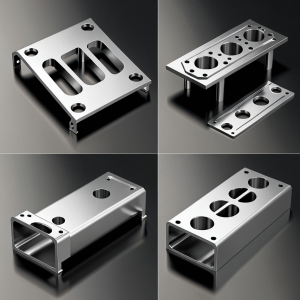
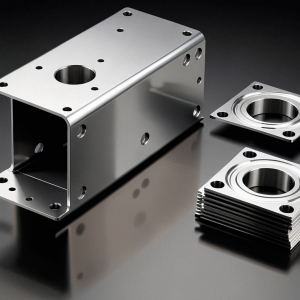
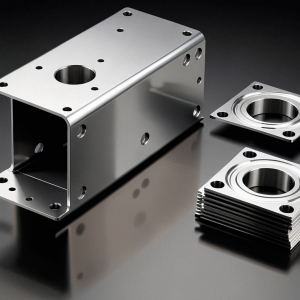
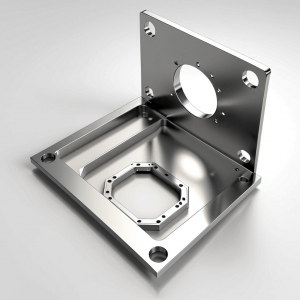
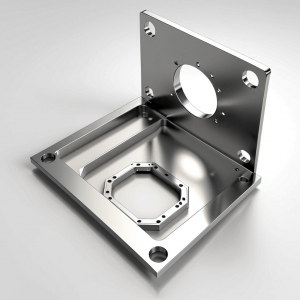
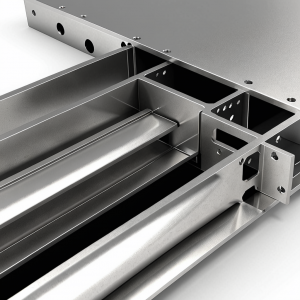
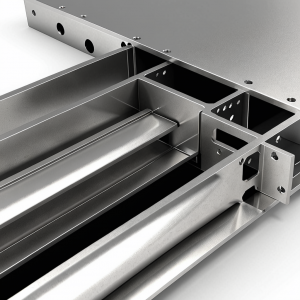
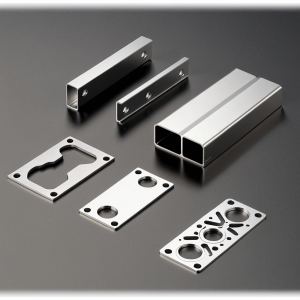
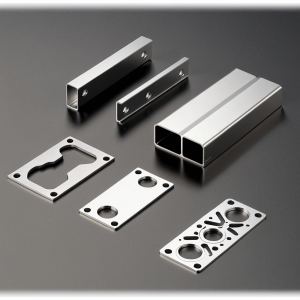
Why Choose GCH
We take an approach that aims to meet your customized needs. We aim to provide long-term prototype overmolding solutions to engineering experts and project managers from design to production. GCH combines cost-effective mold tooling with tech-driven overmolding services that help to make high-quality parts.


No MOQ
No minimum order requirement helps move plastic molded parts from design to production in a fast turnaround and supports your on-demand molding manufacturing needs with reduced injection molding cost.


Tight Tolerance and High Quality
Our plastic injection molding process includes vital design considerations to improve moldability and enhance aesthetic appearance. GCH delivers plastic injection molded parts of varying sizes and complexities. Our standard tolerances are defined by ISO 2768 standards, helping us meet tight tolerance requirements.


High Efficiency
With certified domestic factories and a strong supply chain system, we accelerate the product development cycle and bridge the production of your injection molded parts as fast as possible.


Injection Molding Specialists
Working with our experts having 10+ years of experience in the injection molding industry, efficiently complete a turnaround from prototyping to production.
How Custom Plasma Cut Works?
The injection molding process involves feeding raw plastic materials into an injection molding machine, melting them down, and then injecting them into an aluminum or steel mold. Upon cooling, a production-grade thermoplastic part is formed and ejected for further use or assembly.
Gallery of Plasma Cut Parts
Dive into GCH’s extensive gallery that showcases some of our completed injection molded parts and take confidence that we can create your injection molding project according to your strict specifications.
The FAQ
Frequently Asked Questions
Our mold-making process includes 6 steps:
Step 1: Production arrangement: Determine all of the requirements and arrange the production.
Step 2: DFM report analysis: Provide free but detailed production DFM report for further feasibility analysis.
Step 3: Production the mold: Put the mold into production and provide the Tooling Schedule form for the whole cycle for clients to check the process at any time.
Step 4: Free sample to test: Put the mold into production and provide the Tooling Schedule form for the whole cycle for clients to check the process at any time.
Step 5: Mass production:Client confirms the samples are qualified, then officially proceed with the subsequent production.
Step 6: Mold saving: Production is completed and delivered after quality inspection. Mold will be cleaned and properly stored for the next round of parts production.
Tolerances are crucial in injection molding; without proper specification and control, assembly issues can arise. At GCH, we adhere to the ISO 2068-c standard for molding tolerances, but can accommodate tighter specifications if needed.
We have no minimum order requirement. However, larger quantities will yield more competitive pricing.
Once an order is placed, mold design and creation typically take around 35 days, with an additional 3-5 days for the production of the molded parts.
The cost of our services varies based on several factors such as component size, mold complexity, number of cavities, material type, and post-processing requirements. We provide quotes after analyzing these factors on our platform.
At GCH, we offer a wide range of thermoplastic and thermosetting materials suitable for various applications. Some common materials include ABS, Polycarbonate, Polypropylene, and TPE. For a full list of materials or custom material requests, please contact our customer service.
Yes, GCH offers rapid prototyping services. This allows you to test and verify your design before committing to large-scale production.
Latest Posts
The Challenges Of Titanium CNC Machining And How To Overcome Them
Expert Titanium CNC Machining – Precision CNC machining of titanium parts for aerospace, medical, and industrial applications. High-quality custom parts manufacturing.
Top Challenges in Machining Titanium Alloys and How to Overcome Them
Titanium alloy machining: Expert precision manufacturing for aerospace, medical, and industrial applications.
The Role Of Automation In High Precision Manufacturing
High precision manufacturing ensures exactness in producing intricate components, utilizing advanced technology for industries like aerospace, automotive, and medical devices.